Low-temperature sintered magnesium titanate ceramic and preparation method thereof
A low-temperature sintering, magnesium titanate technology, applied in the field of material science, can solve the problems of deteriorating the microwave dielectric properties of ceramics, and achieve the effect of reducing the sintering temperature and the dosage
- Summary
- Abstract
- Description
- Claims
- Application Information
AI Technical Summary
Problems solved by technology
Method used
Examples
Example Embodiment
[0045] Example 1:
[0046] Weigh 100 parts of tetrabutyl titanate and dissolve it in acetic acid to form a 1.5 mol / l solution. Weigh 95 parts of magnesium nitrate, 5 parts of calcium nitrate, 1 part of zinc nitrate, 1 part of barium nitrate, and 10 parts of boric acid in absolute ethanol to form a 2.0mol / l solution. At the same time, add 0.01 part of 5% nitric acid. Adjust the pH value of the solution to 4.5, then add 1 part of ethyl orthosilicate, mix and stir, add the prepared acetic acid solution of tetrabutyl titanate. Add 2 parts of deionized water and 5 parts of oleic acid to the above mixed solution, mix and stir evenly. Place the above mixed solution in a water bath at 60°C to obtain a transparent gel; dry the above gel in an oven at 90°C for 18 hours, then put it in a high-alumina crucible and calcinate at 700°C for 2 hours to obtain a white ceramic Powder. Ball mill the above ceramic powder, then add 15 parts of polyvinyl alcohol aqueous solution as a binder, fully
Example Embodiment
[0047] Example 2:
[0048] Weigh 100 parts of tetraethyl titanate and dissolve it in acetic acid to form a 2.0 mol / l solution. Weigh 90 parts of magnesium acetate, 4.5 parts of calcium acetate, 3 parts of zinc acetate, 3 parts of barium acetate, and 8 parts of boric acid in absolute ethanol to form a 1.5mol / l solution, and add 5 parts of acetic acid to adjust the pH of the solution. Adjust to 5.0, then add 5 parts of ethyl orthosilicate, mix and stir, add the prepared acetic acid solution of tetraethyl titanate. Add 10 parts of deionized water and 3 parts of polyethylene glycol to the above mixed solution, mix and stir evenly. Place the above mixed solution in a 60°C water bath to obtain a transparent gel; dry the above gel in an oven at 95°C for 12 hours, then put it in a high-alumina crucible, and calcinate at 750°C for 2 hours to obtain a white ceramic Powder. The above ceramic powder is ball milled, and then 16 parts of polyvinyl alcohol aqueous solution are added as a bi
Example Embodiment
[0049] Example 3:
[0050] Weigh 70 parts of tetrabutyl titanate and 30 parts of titanium tetrachloride and dissolve in acetic acid to form a 1.5 mol / l solution. Weigh 70 parts of magnesium nitrate, 22 parts of magnesium chloride, 4 parts of calcium nitrate, 0.7 parts of calcium chloride, 10 parts of zinc nitrate, 10 parts of zinc chloride, 10 parts of barium nitrate, 10 parts of barium chloride, and 50 parts of boric acid. In the water ethanol, a 3.0mol / l solution is formed. At the same time, 0.01 parts of 5% nitric acid and 0.01 parts of 5% hydrochloric acid are added to adjust the pH of the solution to 4.3, and then 20 parts of ethyl orthosilicate are added. After mixing and stirring, add the acetic acid solution of the prepared titanium compound. Add 40 parts of deionized water and 5 parts of polyvinyl butyral to the above mixed solution, mix and stir evenly. Place the above mixed solution in a water bath at 60°C to obtain a transparent gel; dry the above gel in an oven at
PUM
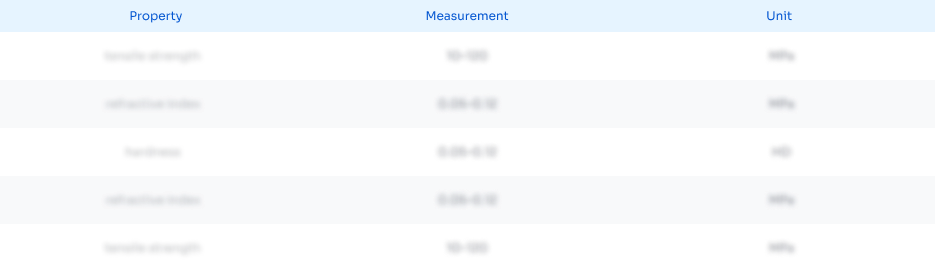
Abstract
Description
Claims
Application Information
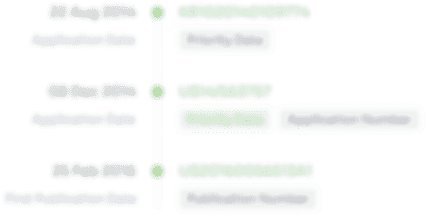
- R&D Engineer
- R&D Manager
- IP Professional
- Industry Leading Data Capabilities
- Powerful AI technology
- Patent DNA Extraction
Browse by: Latest US Patents, China's latest patents, Technical Efficacy Thesaurus, Application Domain, Technology Topic.
© 2024 PatSnap. All rights reserved.Legal|Privacy policy|Modern Slavery Act Transparency Statement|Sitemap