Preparation method of Ta2AlC-Ta4AlC3 composite material
A ta2alc-ta4alc3, composite material technology, applied in the field of new structural material preparation, can solve the problems of inability to inquire about SPS sintering synthesis preparation, few reports on synthesis preparation, etc., and achieve the effects of short synthesis time, lower sintering temperature, and simple process
- Summary
- Abstract
- Description
- Claims
- Application Information
AI Technical Summary
Problems solved by technology
Method used
Image
Examples
Embodiment 1
[0018] Embodiment 1: a kind of Ta 2 AlC-Ta 4 AlC 3 The preparation method of composite material comprises the following steps:
[0019] (1) Using tantalum powder, aluminum powder and tantalum carbide powder as raw materials, according to the molar ratio of Ta:Al:TaC =1:1.4:1 and adding tantalum carbide powder with a mass fraction of 10%;
[0020] (2) Put the above ingredients into a ball mill tank, and wet mix them on a planetary ball mill for 15 hours;
[0021] (3) Adopt rotary evaporator to dry mixed material, then put into graphite abrasive tool and carry out pre-compression, pre-compression pressure is 20Mpa;
[0022] (4) The mold was placed in a spark plasma sintering furnace, heated to 1500°C at a heating rate of 200°C / min under the protection of Ar gas, and kept at a pressure of 500MPa for 5min. After the heat preservation is completed, cool down to room temperature with the furnace to obtain Ta 2 AlC-Ta 4 AlC 3 Composite bulk ceramics.
Embodiment 2
[0023] Embodiment 2: a kind of Ta 2 AlC-Ta 4 AlC 3 The preparation method of composite material comprises the following steps:
[0024] (1) Using tantalum powder, aluminum powder and tantalum carbide powder as raw materials, according to the molar ratio of Ta:Al:TaC =1:1.4:1 and adding tantalum carbide powder with a mass fraction of 20%;
[0025] (2) Put the above ingredients into a ball mill tank, and wet mix them on a planetary ball mill for 15 hours;
[0026] (3) Adopt rotary evaporator to dry the mixed material, then put it into the graphite abrasive tool and carry out pre-compression, the pre-compression pressure is 20Mpa;
[0027] (4) The mold was placed in a spark plasma sintering furnace, heated to 1500°C at a heating rate of 200°C / min under the protection of Ar gas, and kept at a pressure of 500MPa for 5min. After the heat preservation is completed, cool down to room temperature with the furnace to obtain Ta 2 AlC-Ta 4 AlC 3 Composite bulk ceramics.
Embodiment 3
[0028] Embodiment 3: a kind of Ta 2 AlC-Ta 4 AlC 3 The preparation method of composite material comprises the following steps:
[0029] (1) Using tantalum powder, aluminum powder and tantalum carbide powder as raw materials, according to the molar ratio of Ta:Al:TaC =1:1.4:1 and adding tantalum carbide powder with a mass fraction of 30%;
[0030] (2) Put the above-mentioned ingredients into a ball mill tank, and wet mix them on a planetary ball mill for 15 hours;
[0031] (3) Adopt rotary evaporator to dry the mixed material, then put it into the graphite abrasive tool and carry out pre-compression, the pre-compression pressure is 20Mpa;
[0032](4) The mold was placed in a spark plasma sintering furnace, heated to 1500°C at a heating rate of 200°C / min under the protection of Ar gas, and kept at a pressure of 500MPa for 5min. After the heat preservation is completed, cool down to room temperature with the furnace to obtain Ta 2 AlC-Ta 4 AlC 3 Composite bulk ceramics.
...
PUM
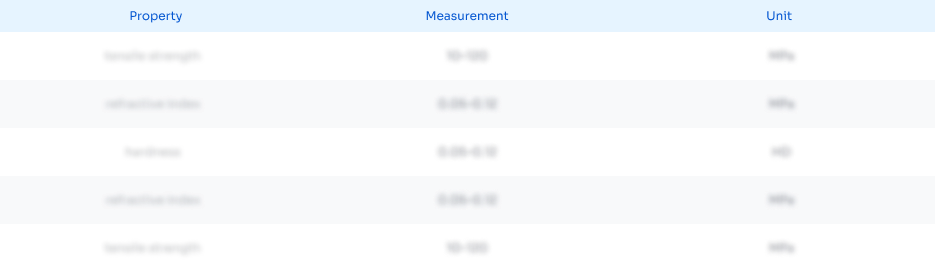
Abstract
Description
Claims
Application Information
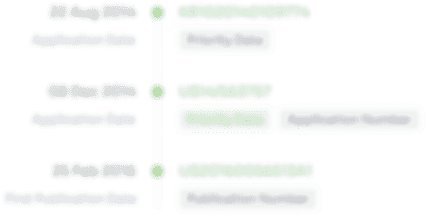
- R&D Engineer
- R&D Manager
- IP Professional
- Industry Leading Data Capabilities
- Powerful AI technology
- Patent DNA Extraction
Browse by: Latest US Patents, China's latest patents, Technical Efficacy Thesaurus, Application Domain, Technology Topic.
© 2024 PatSnap. All rights reserved.Legal|Privacy policy|Modern Slavery Act Transparency Statement|Sitemap