Method for preparing high-performance sintered Nd-Fe-B magnet
A neodymium iron boron and magnet technology, used in magnetic objects, inductance/transformer/magnet manufacturing, magnetic materials, etc., can solve the problems that vacuum and pressure cannot be achieved, pressure cannot be applied, and vacuum cannot be evacuated, and the sintering temperature cannot be reduced. , The effect of increasing magnet density and uniform distribution
- Summary
- Abstract
- Description
- Claims
- Application Information
AI Technical Summary
Problems solved by technology
Method used
Image
Examples
Example Embodiment
[0017] Example 1
[0018] The selected magnet composition is Nd 13.5 Dy 0.5 Fe 79.97 B 6.03 , The vacuum melting furnace smelts alloy, the vacuum degree is 10 -3 Pa, the alloy is casted using rapid-setting cast sheet technology, the thickness of the SC sheet is about 0.25~0.35mm. After hydrogen breaking and jet milling, it is made into powder. The powder is loosely packed and subjected to magnetic field orientation and compaction. The loose packed density is about 1.5g / cm 3 , The orientation field is greater than 1.5T. Next is the sintering stage, which can be sintered in two ways: one is the current sintering method, first vacuuming, and then continuing vacuuming and exhausting and heating stages. After reaching the sintering temperature, keep it for 3 hours, and then blow into the room temperature high purity Argon air cooling, magnet number is set to 1 # ; The other is the sintering method described in the present invention, first vacuuming, and then continuing vacuuming and e
Example Embodiment
[0021] Example 2
[0022] The selected magnet composition is Nd 13.5 Dy 0.5 Fe 79.97 B 6.03 , The vacuum melting furnace smelts alloy, the vacuum degree is 10 -3 Pa, the alloy is casted using rapid-setting cast sheet technology, the thickness of the SC sheet is about 0.25~0.35mm. After hydrogen breaking and jet milling, it is made into powder. The powder is loosely packed and subjected to magnetic field orientation and compaction. The loose packed density is about 1.5g / cm 3 , The orientation field is greater than 1.5T. Next is the sintering stage, which is sintered in two ways: one is to vacuum first, and then to continue vacuuming and exhausting and heating up. After the exhaust gas is over, the vacuum is stopped before reaching the sintering temperature and the high Pure Ar gas pressurization, pressure 10Mpa, sintering at 1080 ℃ sintering temperature, holding for 3 hours, at the end of sintering, pass in room temperature high-purity Ar gas for air cooling, the magnet number is
PUM
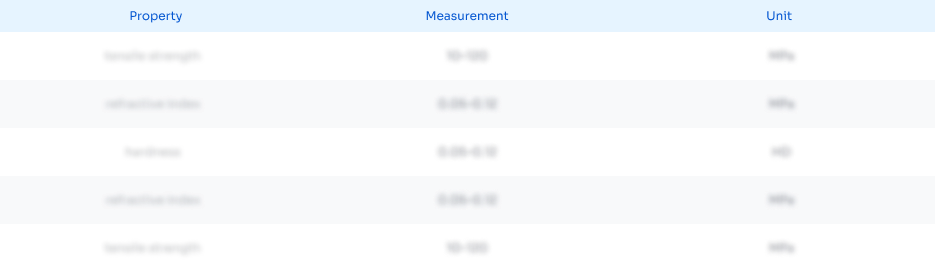
Abstract
Description
Claims
Application Information
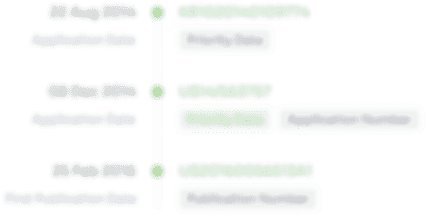
- R&D Engineer
- R&D Manager
- IP Professional
- Industry Leading Data Capabilities
- Powerful AI technology
- Patent DNA Extraction
Browse by: Latest US Patents, China's latest patents, Technical Efficacy Thesaurus, Application Domain, Technology Topic.
© 2024 PatSnap. All rights reserved.Legal|Privacy policy|Modern Slavery Act Transparency Statement|Sitemap