Method for preparing industrial molybdenum trioxide by roasting ammonia leaching residue
A technology of molybdenum trioxide and ammonia leaching slag, which is applied in the direction of improving process efficiency, etc., can solve the problems of high consumption of raw and auxiliary materials, poor economic benefits, and high labor intensity, so as to reduce equipment material requirements and reduce the cost of recycling molybdenum , Improve the effect of metal recovery rate
- Summary
- Abstract
- Description
- Claims
- Application Information
AI Technical Summary
Benefits of technology
Problems solved by technology
Method used
Examples
Embodiment 1
[0014] The ammonia leaching slag with molybdenum mass percentage content of 7% and molybdenum concentrate with molybdenum mass percentage content of 57% are mixed evenly according to the mass ratio of 1:4, then the mixture is placed in the rotary kiln, and the roasting temperature is Calcined at 450°C for 8 hours to obtain industrial molybdenum trioxide.
[0015] After testing (there is an error in actual detection), the mass percentage of Mo in the industrial molybdenum trioxide prepared by the present embodiment is 44.8%, the mass percentage of P is 0.016%, and the mass percentage of S is 0.037%, which meets Requirements for the production of ammonium molybdate, ferromolybdenum and other products.
Embodiment 2
[0017] The ammonia leaching slag that is 21% by mass of molybdenum and the molybdenum concentrate that is 57% by mass of molybdenum are mixed evenly according to the mass ratio of 1:4, then the mixture is placed in a rotary kiln, and the roasting temperature is Calcined at 500°C for 7 hours to obtain industrial molybdenum trioxide.
[0018] After testing (there is an error in actual detection), the mass percentage of Mo in the industrial molybdenum trioxide prepared by the present embodiment is 46.5%, the mass percentage of P is 0.02%, and the mass percentage of S is 0.05%, which meets Requirements for the production of ammonium molybdate, ferromolybdenum and other products.
Embodiment 3
[0020] The ammonia leaching slag that is 14% by mass of molybdenum and the molybdenum concentrate that is 57% by mass of molybdenum are mixed evenly according to the mass ratio of 1:5, then the mixture is placed in a rotary kiln, and the roasting temperature is Calcined at 680°C for 5 hours to obtain industrial molybdenum trioxide.
[0021] After testing (there is an error in actual detection), the mass percentage of Mo in the industrial molybdenum trioxide prepared by the present embodiment is 45.3%, the mass percentage of P is 0.012%, and the mass percentage of S is 0.04%, which meets Requirements for the production of ammonium molybdate, ferromolybdenum and other products.
PUM
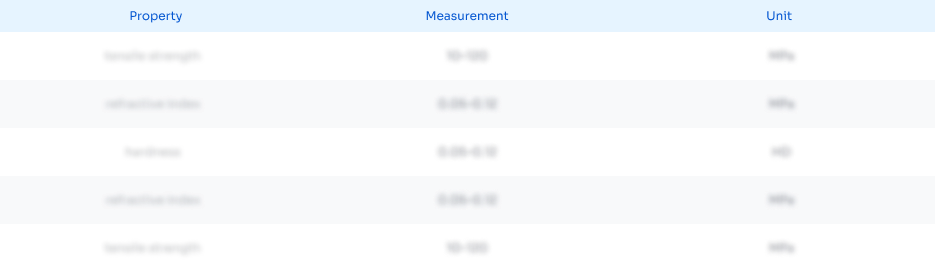
Abstract
Description
Claims
Application Information
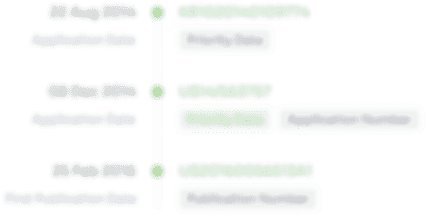
- R&D Engineer
- R&D Manager
- IP Professional
- Industry Leading Data Capabilities
- Powerful AI technology
- Patent DNA Extraction
Browse by: Latest US Patents, China's latest patents, Technical Efficacy Thesaurus, Application Domain, Technology Topic.
© 2024 PatSnap. All rights reserved.Legal|Privacy policy|Modern Slavery Act Transparency Statement|Sitemap