Isostactic pressing method and isostactic pressing system
A pressure forming and pressure cavity technology, applied in the field of pressure equalizing forming methods and systems thereof, can solve the problems of inability to improve yield, pressure and heat of imprints, unevenness, etc.
- Summary
- Abstract
- Description
- Claims
- Application Information
AI Technical Summary
Problems solved by technology
Method used
Image
Examples
Embodiment Construction
[0039] see figure 1 , which is a schematic diagram of the first embodiment of the isostatic molding system of the present invention. In the figure, an isostatic molding system 1 includes an isostatic molding device 2 , a temperature control device 3 and a pressure device 4 .
[0040]The isostatic molding device 2 includes a first cavity 20 , a first template 22 and a second template 23 . The first cavity 20 is disposed on one side of a mold machine 5 , and the first cavity 20 has a first opening 201 . In the first cavity 201 lower than the first opening 201 , a first heat conduction film 24 is disposed, and the first heat conduction film 24 closes the first cavity 20 to form a first airtight pressure chamber 21 . A first liquid inlet and outlet 25 is provided anywhere around the first airtight pressure chamber 21 . The first template 22 is arranged on the first heat conducting film 24 , and the second template 23 is arranged on the other side of the mold machine 5 . An imp...
PUM
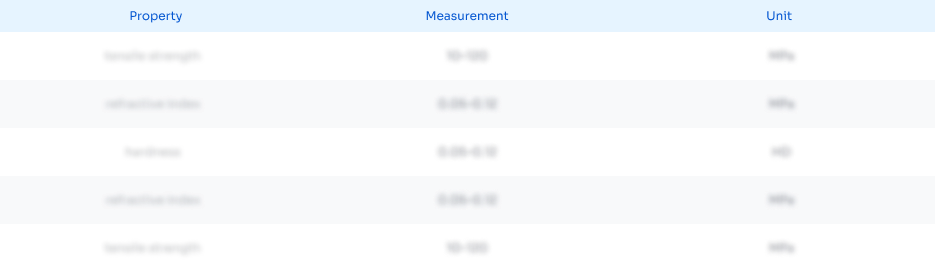
Abstract
Description
Claims
Application Information
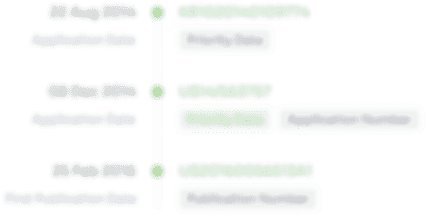
- R&D Engineer
- R&D Manager
- IP Professional
- Industry Leading Data Capabilities
- Powerful AI technology
- Patent DNA Extraction
Browse by: Latest US Patents, China's latest patents, Technical Efficacy Thesaurus, Application Domain, Technology Topic.
© 2024 PatSnap. All rights reserved.Legal|Privacy policy|Modern Slavery Act Transparency Statement|Sitemap