Process for preparing chloroethylene from ethane
A technology of vinyl chloride and ethane, applied in the field of chemical engineering, can solve the problems of wide application range of vinyl chloride, high production cost, energy shortage, etc., and achieve the effect of broadening the source of raw materials, reducing energy consumption, and promoting rational utilization
- Summary
- Abstract
- Description
- Claims
- Application Information
AI Technical Summary
Problems solved by technology
Method used
Examples
Example Embodiment
[0022] Example 1
[0023] The reactor uses a fluidized bed with a height of 7m and a diameter of 1m, using Al 2 O 3 As carrier, CuC1 2 As a catalyst, the amount of catalyst is 1g / m 2 , The catalyst is activated with HCl and air before the reaction. The activation method is to use HCl and air at a volume ratio of 3:5, where the HCl flow rate is 180mL / min, and the mixture is heated to the reaction temperature and activated at this temperature for 0.5h; At the beginning of the reaction, the heated ethane and hydrogen chloride or hydrocarbon chloride and oxygen from the air separation unit are proportional to V(C 2 H 6 ):V(HCl):V(O 2 )=2:1:7 are sent to the reactor for reaction together, the reaction pressure is 5Mpa, the reaction temperature is 550℃, and the reaction time is 120h. The produced vinyl chloride is condensed at 50℃. The ethane conversion rate in this process reaches 94.8%. The single-pass yield of ethylene can reach 70.9%.
Example Embodiment
[0024] Example 2
[0025] The reactor uses a fluidized bed with a height of 7m and a diameter of 1m, using Al 2 O 3 As carrier, CuC1 2 As a catalyst, the amount of catalyst is 2.5g / m 2 The catalyst is activated with HCl and air before the reaction. The activation method is to use a volume ratio of HCl to air of 3:5, where the HCl flow rate is 180 mL / min, and the mixture is heated to the reaction temperature and activated at this temperature for 40 minutes. At the beginning of the reaction, the heated ethane and hydrogen chloride or hydrocarbon chlorides and oxygen from the air separation unit are proportionally V(C 2 H 6 ):V(HCl):V(O 2 )=1:2:1 and sent to the reactor together for reaction, the pressure is 6Mpa, the reaction temperature is 450°C, the reaction time is 100h, and the produced vinyl chloride is condensed at 50°C. The conversion of ethane in this process reached 97.8%, and the single-pass yield of vinyl chloride reached 96.8%.
Example Embodiment
[0026] Example 3
[0027] The reactor uses a fluidized bed with a height of 7m and a diameter of 1m, using Al 2 O 3 As carrier, CuC1 2 As a catalyst, the amount of catalyst is 2g / m 2 The catalyst is activated with HCl and air before the reaction. The activation method is to use a volume ratio of HCl to air of 3:5, where the HCl flow rate is 180 mL / min, and the mixture is heated to the reaction temperature and activated at this temperature for 1 hour. At the beginning of the reaction, the heated ethane and hydrogen chloride or hydrocarbon chlorides and oxygen from the air separation unit are proportionally V(C 2 H 6 ):V(HCl):V(O 2 )=1:3:5 and sent to the reactor together for reaction, the pressure is 4Mpa, the reaction temperature is 500℃, the reaction time is 90h, the produced vinyl chloride is condensed at 50℃, the ethane conversion rate in this process reaches 95.7%, chlorine The single-pass yield of ethylene reached 87.6%.
PUM
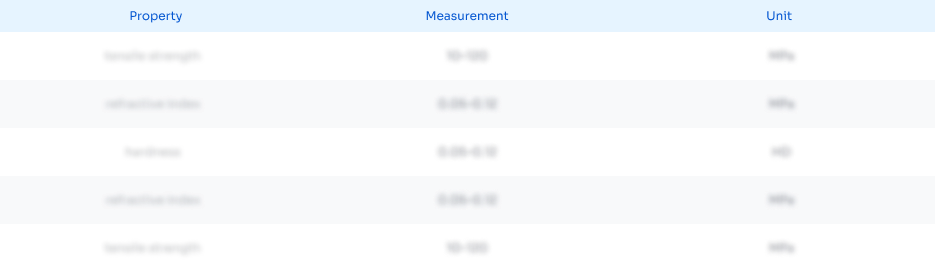
Abstract
Description
Claims
Application Information
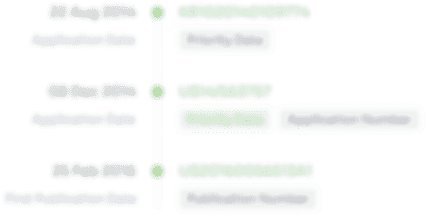
- R&D Engineer
- R&D Manager
- IP Professional
- Industry Leading Data Capabilities
- Powerful AI technology
- Patent DNA Extraction
Browse by: Latest US Patents, China's latest patents, Technical Efficacy Thesaurus, Application Domain, Technology Topic.
© 2024 PatSnap. All rights reserved.Legal|Privacy policy|Modern Slavery Act Transparency Statement|Sitemap