Gas-solid separation ceramic material and preparation method thereof
A technology of gas-solid separation and ceramic materials, applied in the field of ceramic filter materials, can solve the problems of dust dew point corrosion, power consumption, high economic cost, etc., achieve high filtration efficiency and porosity, save production costs, and excellent comprehensive performance.
- Summary
- Abstract
- Description
- Claims
- Application Information
AI Technical Summary
Problems solved by technology
Method used
Image
Examples
Embodiment 1
[0026] (1) Preparation of raw materials
[0027] Add 5g of polyacrylamide into 5L of water to prepare an aqueous fiber dispersant solution with a mass concentration of 1g / L;
[0028] Mix 21g of kaolin, 4.5g of calcium oxide, 4.5g of magnesium oxide, and 70g of aluminum silicate fiber at a solid-to-liquid weight ratio of 1:50, then add them to the aqueous fiber dispersant solution, mix and stir evenly to obtain a slurry;
[0029] (2) Sample molding and firing
[0030] Connect the connection hole on the cylindrical porous metal outer mold (inner diameter = 127mm) with the liquid storage tank and the vacuum pump, and the inner mold (inner diameter = 71mm, wall thickness = 2mm, height = 700mm) is placed in the outer mold, and the openings of the two The end is sealed by the flange edge, and at the same time, a 100-mesh stainless steel filter is spread on the inner wall of the porous metal inner mold, and then the mixed slurry is slowly injected into the porous metal inner mold; th
Embodiment 2
[0038] (1) Preparation of raw materials
[0039]Add 15g of polyacrylamide into 15L of water to prepare an aqueous fiber dispersant solution with a mass volume concentration of 1g / L;
[0040] Mix 23g of kaolin, 0.5g of calcium oxide, 2.5g of magnesium oxide and 77g of aluminum silicate fiber according to the solid-to-liquid weight ratio of 1:150, then add them to the above fiber dispersant aqueous solution, mix and stir evenly to obtain a slurry;
[0041] (2) Sample molding and firing
[0042] Connect the connection hole on the cylindrical porous metal outer mold with the liquid storage tank and the vacuum pump, place the inner mold in the outer mold, and seal the opening ends of the two through the flange edge, and lay a 100-mesh stainless steel filter in the porous metal The inner wall of the mold, and then slowly inject the mixed slurry into the porous metal inner mold; turn on the vacuum pump, and at the same time make the cylindrical porous metal mold rotate around the cen
Embodiment 3
[0050] (1) Preparation of raw materials
[0051] Add 15g of polyacrylamide into 10L of water to prepare an aqueous fiber dispersant solution with a mass volume concentration of 1.5g / L;
[0052] Mix 12g of kaolin, 4g of calcium oxide, 4g of magnesium oxide and 80g of aluminum silicate fiber according to the solid-to-liquid weight ratio of 1:100, then add them to the above fiber dispersant aqueous solution, mix and stir evenly to obtain a slurry;
[0053] (2) Sample molding and firing
[0054] Connect the connection hole on the cylindrical porous metal outer mold with the liquid storage tank and the vacuum pump, place the inner mold in the outer mold, and seal the opening ends of the two through the flange edge, and lay a 100-mesh stainless steel filter in the porous metal The inner wall of the mould, and then slowly inject the mixed slurry into the porous metal inner mold; turn on the vacuum pump, and at the same time make the cylindrical porous metal mold rotate around the cen
PUM
Property | Measurement | Unit |
---|---|---|
Flexural strength | aaaaa | aaaaa |
Filter resistance | aaaaa | aaaaa |
Average apparent density | aaaaa | aaaaa |
Abstract
Description
Claims
Application Information
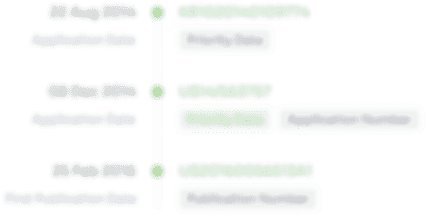
- R&D Engineer
- R&D Manager
- IP Professional
- Industry Leading Data Capabilities
- Powerful AI technology
- Patent DNA Extraction
Browse by: Latest US Patents, China's latest patents, Technical Efficacy Thesaurus, Application Domain, Technology Topic.
© 2024 PatSnap. All rights reserved.Legal|Privacy policy|Modern Slavery Act Transparency Statement|Sitemap