Preparation method of refining agent for smelting fly ash doped aluminum alloy
A refining agent and fly ash technology, used in the smelting of high-strength aluminum alloy profiles and the processing of aluminum alloy materials, can solve the problem of poor electrical conductivity, thermal conductivity and corrosion resistance of finished products, affecting the performance of alloy castings, and the proportion of oxidized impurities. Advanced problems, to achieve the effect of improving quality and processing performance, improving yield, and improving mechanical properties
- Summary
- Abstract
- Description
- Claims
- Application Information
AI Technical Summary
Problems solved by technology
Method used
Examples
Embodiment Construction
[0013] The present invention will be further described below in conjunction with embodiment, but not limited to following embodiment.
[0014] A method for preparing a refining agent for aluminum alloy smelting mixed with fly ash, comprising the following steps: it is prepared from the following raw materials by weight (kg): lithium chloride 7, tree ash 5, phosphorite slag 7, pulverized coal Ash 8, zinc chloride 7, calcium fluoride 4, sodium nitrate 4, sodium fluorosilicate 9, sodium sulfate 4, aluminum chloride 6, potassium carbonate 4, zeolite 9, NaBF 4 6. Sodium chloride 4. Calcium carbonate 7. Na 2 TiF 6 9. NaF 7, after mixing the tree ash, phosphate rock slag, and fly ash in the parts by weight, they are wrapped in zinc chloride to form granules, and the granules are soaked in 12-15% sulfuric acid for 3-4 hours, washed with deionized water, and then Soak in 12-15% sodium hydroxide solution for 3-4 hours, then wash with deionized water until neutral, then heat to 350-36...
PUM
Property | Measurement | Unit |
---|---|---|
particle diameter | aaaaa | aaaaa |
Abstract
Description
Claims
Application Information
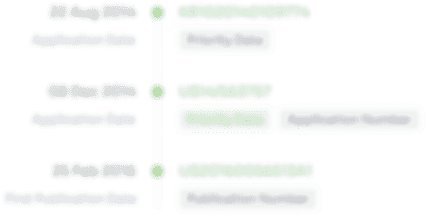
- R&D Engineer
- R&D Manager
- IP Professional
- Industry Leading Data Capabilities
- Powerful AI technology
- Patent DNA Extraction
Browse by: Latest US Patents, China's latest patents, Technical Efficacy Thesaurus, Application Domain, Technology Topic.
© 2024 PatSnap. All rights reserved.Legal|Privacy policy|Modern Slavery Act Transparency Statement|Sitemap