Thermally conductive insulating material for high-power LED substrate and preparation method thereof
A technology for thermally conductive insulating materials and LED substrates, applied in the field of material chemistry, can solve the problems of poor physical and thermal conductivity of thermally conductive resin materials, poor bending and kink resistance, and poor compression and shock resistance. The branch copolymerization reaction is sufficient, the rate is fast, and the effect of increasing stiffness
- Summary
- Abstract
- Description
- Claims
- Application Information
AI Technical Summary
Benefits of technology
Problems solved by technology
Method used
Examples
Embodiment 1
[0032] This embodiment provides a thermally conductive insulating material for a high-power LED substrate, and the thermally conductive insulating material for a high-power LED substrate is prepared through the following steps:
[0033] (1) In parts by mass, add 30 parts of silicon oxide powder with an average particle size of 10nm to 3 parts of graft modifier maleic anhydride, then add 0.1 part of dispersant to polyacrylamide, and stir for 10 to 15 minutes. Then use ultrasonic dispersion for 20 to 30 minutes to disperse the nano-silica powder in the mixed solvent of maleic anhydride and polyacrylamide to form an emulsion-like dispersion;
[0034] (2) adding the emulsion-like dispersion prepared in the above step (1) to ultrasonic spray drying equipment for spray drying to prepare a powdery composite material containing nano-silicon oxide;
[0035] (3) Add the powdered composite material prepared in the above step (2) together with 7 parts of polypropylene resin powder from the f
Embodiment 2
[0042] This embodiment also provides a thermally conductive insulating material for a high-power LED substrate. The thermally conductive insulating material for a high-power LED substrate is prepared through the following steps:
[0043] (1) In parts by mass, add 80 parts of alumina powder with an average particle size of 30nm to 20 parts of graft modifier oleic acid, then add 10 parts of dispersant sodium lauryl sulfate, and stir for 10 to 15 minutes, and then use ultrasonic dispersion for 20 to 30 minutes to disperse the nano-alumina powder in the mixed solvent of oleic acid and sodium lauryl sulfate to form an emulsion-like dispersion;
[0044] (2) adding the emulsion-like dispersion prepared in the above step (1) to ultrasonic spray drying equipment for spray drying to prepare a powdery composite material containing nano-silicon oxide;
[0045] (3) Add the powdered composite material prepared in the above step (2) together with 40 parts of polyethylene resin powder from the f
Embodiment 3
[0052] This embodiment also provides a thermally conductive insulating material for a high-power LED substrate. The thermally conductive insulating material for a high-power LED substrate is prepared through the following steps:
[0053] (1) In parts by mass, add 30 parts of magnesium oxide powder with an average particle size of 50nm to 20 parts of graft modifier acrylic acid, then add 10 parts of dispersant as fatty acid polyethylene glycol ester, and stir for 10 to 15 minutes , and then use ultrasonic dispersion for 20 to 30 minutes to disperse the nano magnesium oxide powder in a mixed solvent of acrylic acid and fatty acid polyethylene glycol ester to form an emulsion-like dispersion;
[0054] (2) adding the emulsion-like dispersion prepared in the above step (1) to ultrasonic spray drying equipment for spray drying to prepare a powdery composite material containing nano-magnesia;
[0055] (3) Add the powdered composite material prepared in the above step (2) together with 40
PUM
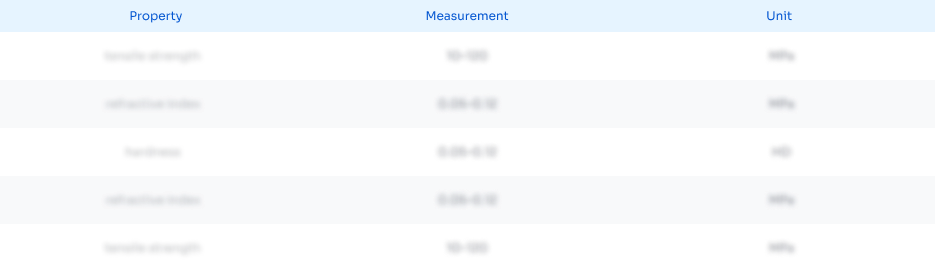
Abstract
Description
Claims
Application Information
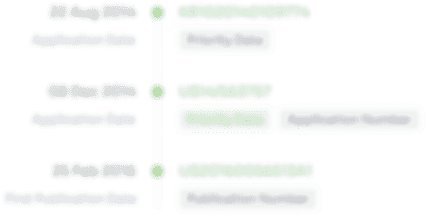
- R&D Engineer
- R&D Manager
- IP Professional
- Industry Leading Data Capabilities
- Powerful AI technology
- Patent DNA Extraction
Browse by: Latest US Patents, China's latest patents, Technical Efficacy Thesaurus, Application Domain, Technology Topic.
© 2024 PatSnap. All rights reserved.Legal|Privacy policy|Modern Slavery Act Transparency Statement|Sitemap