Reinforcing eyelet fabric and preparation method thereof
A mesh cloth and reinforcement technology, applied in the field of mesh cloth, can solve the problems of melting, affecting the pressure resistance performance of high-pressure hoses, and reducing the overall strength, and achieve the effects of improving service life, improving pressure resistance and improving pressure resistance.
- Summary
- Abstract
- Description
- Claims
- Application Information
AI Technical Summary
Benefits of technology
Problems solved by technology
Method used
Examples
Embodiment 1
[0016] Adhesive layer preparation: first add 70 parts by weight of water to the reactor, add 2.0 parts by weight of sodium hydroxide with a concentration of 12%, then add 16 parts by weight of formaldehyde with a concentration of 37% and 8 parts by weight of resorcinol Add it into the reaction kettle, stir and react for 9 hours at a temperature of 23°C to obtain the intermediate liquid; then take the intermediate liquid and add the same weight of butylpyridine latex as the intermediate liquid, stir for 2 hours and then place it for 1.5 hours to react;
[0017] Dipping: Put the glue solution obtained from the above reaction into the dipping tank, heat it to 150°C, and then weave the nylon 6 chemical fiber with a warp and weft density of 35 strands / 5cm and 26 strands / 5cm respectively. Long filaments between centimeters are woven and arranged to make the fiber surface impregnated with a glue layer, and the glue dipping time is controlled at 3 minutes. The adhesive layer that ca
Embodiment 2
[0019] Adhesive layer preparation: first add 75 parts by weight of water to the reactor, add 2.5 parts by weight of sodium hydroxide with a concentration of 12%, then add 17 parts by weight of formaldehyde with a concentration of 37% and 6 parts by weight of resorcinol Add it into the reaction kettle, stir and react for 10 hours at a temperature of 24°C to obtain the intermediate liquid; then take the intermediate liquid and add butylpyridine latex in the same weight part as the intermediate liquid, stir for 2.5 hours and then place it for 2.0 hours to react;
[0020] Dipping: put the glue solution obtained from the above reaction into the dipping tank, heat it to 155°C, and then weave the nylon 66 chemical fiber with a warp and weft density of 36 strands / 5 cm and 28 strands / 5 cm, respectively. Long filaments between centimeters are woven and arranged to make the surface of the fiber impregnated with a glue layer, and the dipping time is controlled at 5 minutes. The adhesive
Embodiment 3
[0022] Adhesive layer preparation: first add 72 parts by weight of water to the reactor, add 1.5 parts by weight of sodium hydroxide with a concentration of 12%, then add 15 parts by weight of formaldehyde with a concentration of 37% and 7 parts by weight of resorcinol Add it into the reaction kettle, stir and react for 11 hours at a temperature of 25°C to obtain the intermediate liquid; then take the intermediate liquid and add butylpyridine latex in the same weight part as the intermediate liquid, stir for 3 hours and then place it for 2.5 hours to react;
[0023] Dipping: Put the glue obtained from the above reaction into the dipping tank, heat it to 160°C, and then weave the nylon 6 chemical fiber with a warp and weft density of 37 strands / 5cm and 27 strands / 5cm respectively. Long filaments between centimeters are woven and arranged to make the surface of the fiber impregnated with a glue layer, and the dipping time is controlled at 4 minutes. The adhesive layer that can
PUM
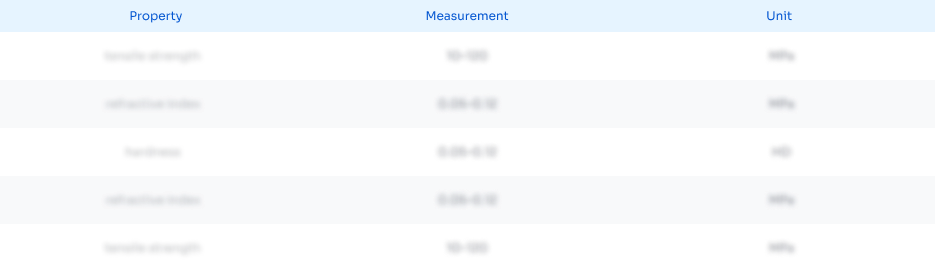
Abstract
Description
Claims
Application Information
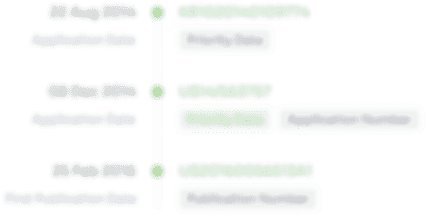
- R&D Engineer
- R&D Manager
- IP Professional
- Industry Leading Data Capabilities
- Powerful AI technology
- Patent DNA Extraction
Browse by: Latest US Patents, China's latest patents, Technical Efficacy Thesaurus, Application Domain, Technology Topic.
© 2024 PatSnap. All rights reserved.Legal|Privacy policy|Modern Slavery Act Transparency Statement|Sitemap