Catalyst for selective hydrogenation and olefin removal of reformed generated oil as well as preparation method and application
A technology of reforming to generate oil and catalyst, applied in the direction of selective hydrofining, metal/metal oxide/metal hydroxide catalyst, physical/chemical process catalyst, etc., can solve solvent oil bromine index and copper sheet corrosion Unqualified tests, unqualified bromine index and pickling color of aromatic products, affecting the smooth progress of the separation process, etc., to shorten the start-up time, avoid the hazards of operators and the environment, and reduce the initial activity.
- Summary
- Abstract
- Description
- Claims
- Application Information
AI Technical Summary
Benefits of technology
Problems solved by technology
Method used
Image
Examples
Embodiment 1
[0036] Weigh 0.21g ruthenium trichloride and 0.43g palladium nitrate, dissolve it with deionized water to make the solution concentration 0.5mol / L, and heat it to 40°C. Slowly add oxalic acid to the mixed solution to make the pH 4.0. Stir uniformly, add 98.7g of alumina carrier for impregnation, keep stirring during the impregnation process, after 12h, filter out the impregnated catalyst and dry, slowly increase from room temperature to 120℃, the heating rate is 10℃ / h, under 120℃ Dry at constant temperature for 18h. The dried catalyst was calcined at 500°C for 5 hours to obtain the desired catalyst. The indicators of the catalyst are shown in Table 1, and the eggshell thickness is shown in Photo 1 of the cross section of the catalyst.
[0037] Weigh 20g of catalyst in a fixed-bed reactor with temperature programmed reduction activation, the activation conditions are: hydrogen pressure is 2.0MPa, volumetric space velocity is 1500h -1 , Reducing at 250℃ for 5h, heating rate is 10℃
Embodiment 2
[0039] Weigh 0.35g platinum tetrachloride, 3.80g copper nitrate trihydrate, 11.78g calcium nitrate tetrahydrate, dissolve it with deionized water to make the solution concentration 0.8mol / L, and heat to 70℃, slowly add acetic acid to the mixed solution , To make the pH of 3.0, stir the solution evenly, add 96.8g of alumina carrier to impregnate, keep stirring during the impregnation process, after 18h, filter out the impregnated catalyst and dry, slowly increase from room temperature to 130℃, the heating rate is 10℃ / h, drying at 130℃ for 10h. The dried catalyst is calcined at 450°C for 6 hours to obtain the desired catalyst. The indicators of the catalyst are shown in Table 1, and the eggshell thickness is shown in Photo 2 of the cross section of the catalyst.
[0040] Weigh 20g of catalyst in a fixed bed reactor for temperature-programmed reduction activation, the activation conditions are: hydrogen pressure is 2.5MPa, volumetric space velocity is 800h -1 , Reducing at 180℃ for
Embodiment 3
[0042] Weigh 0.08g palladium chloride, 0.21g chloroplatinic acid, 0.21g ruthenium trichloride, 14.82g flowing water cobalt nitrate, dissolve it with deionized water so that the concentration of the solution is 0.26mol / L, and heat it to 50℃, Slowly add hydrochloric acid to make the pH 1.9, stir the solution evenly, add 96.8g of alumina carrier for impregnation, keep stirring during the impregnation process, after 15h, filter out the impregnated catalyst and dry it, slowly increase from room temperature to 120℃ , The heating rate is 10℃ / h, and it is dried at 120℃ for 15h. The dried catalyst is calcined at 450°C for 12 hours to obtain the desired catalyst. The indicators of the catalyst are shown in Table 1, and the eggshell thickness is shown in the photo 3 of the cross section of the catalyst.
[0043] Weigh 20g of catalyst in a fixed-bed reactor with temperature programmed reduction activation, the activation conditions are: hydrogen pressure is 2.0MPa, volumetric space velocity
PUM
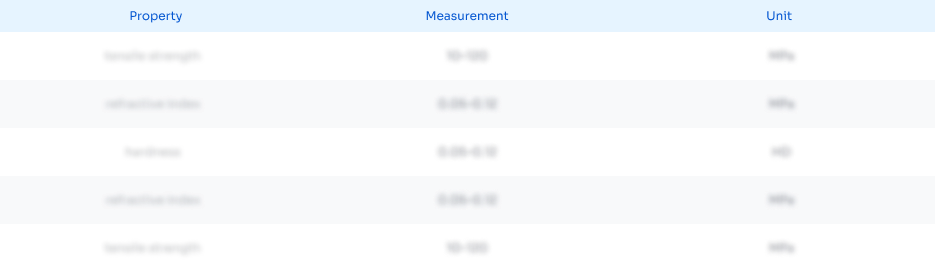
Abstract
Description
Claims
Application Information
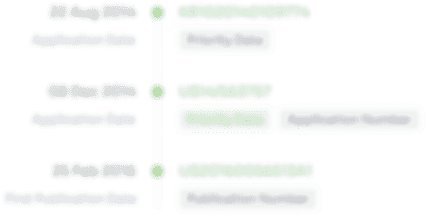
- R&D Engineer
- R&D Manager
- IP Professional
- Industry Leading Data Capabilities
- Powerful AI technology
- Patent DNA Extraction
Browse by: Latest US Patents, China's latest patents, Technical Efficacy Thesaurus, Application Domain, Technology Topic.
© 2024 PatSnap. All rights reserved.Legal|Privacy policy|Modern Slavery Act Transparency Statement|Sitemap