AHS aluminum alloy spectral standard sample and detection method of AHS aluminum alloy component
A spectral standard sample and standard sample technology, applied in the field of AHS aluminum alloy spectral standard sample and AHS aluminum alloy composition detection, to achieve the effect of improving production efficiency and product quality
- Summary
- Abstract
- Description
- Claims
- Application Information
AI Technical Summary
Problems solved by technology
Method used
Image
Examples
Embodiment 1
[0078] Pure aluminum, Al-20wt% Si master alloy, Al-15wt% Fe master alloy, Al-40wt% Cu master alloy, Al-15wt% Mn master alloy, Al-20wt% Ni master alloy and The Al-20wt% Ti master alloy was added into the furnace, and melted and blended at 760° C. to obtain the first alloy melt. Add pure zinc into the first alloy melt according to the composition percentage in Table 1, and stir to obtain the second alloy melt. Add pure magnesium into the second alloy solution according to the composition ratio in Table 1, and stir to obtain the third alloy melt. Add Al-10wt% Sr master alloy to the third alloy solution according to the composition ratio in Table 1 to obtain aluminum alloy melt. Under stirring conditions, hot-top casting is used to cast the aluminum alloy melt. The casting temperature is 735°C, the casting speed is 78mm / min, and the cooling water pressure is 0.06MPa. After the casting, an aluminum alloy with a diameter of 162mm is obtained. Alloy ingots and rods.
[0079] The ch
Embodiment 2
[0095] Pure aluminum, Al-20wt% Si master alloy, Al-15wt% Fe master alloy, Al-40wt% Cu master alloy, Al-15wt% Mn master alloy, Al-20wt% Ni master alloy and The Al-20wt% Ti master alloy was added into the furnace, and melted and blended at 760° C. to obtain the first alloy melt. Add pure zinc into the first alloy melt according to the composition percentage in Table 1, and stir to obtain the second alloy melt. Add pure magnesium into the second alloy solution according to the composition ratio in Table 1, and stir to obtain the third alloy melt. Add Al-10wt% Sr master alloy to the third alloy solution according to the composition ratio in Table 1 to obtain aluminum alloy melt. Under stirring conditions, hot-top casting is used to cast the aluminum alloy melt. The casting temperature is 745°C, the casting speed is 72mm / min, and the cooling water pressure is 0.08MPa. After the casting, an aluminum alloy with a diameter of 162mm is obtained. Alloy ingots and rods.
[0096] The ch
Embodiment 3
[0113] Pure aluminum, Al-20wt% Si master alloy, Al-15wt% Fe master alloy, Al-40wt% Cu master alloy, Al-15wt% Mn master alloy, Al-20wt% Ni master alloy and The Al-20wt% Ti master alloy was added into the furnace, and melted and blended at 760° C. to obtain the first alloy melt. Add pure zinc into the first alloy melt according to the composition percentage in Table 1, and stir to obtain the second alloy melt. Add pure magnesium into the second alloy solution according to the composition ratio in Table 1, and stir to obtain the third alloy melt. Add Al-10wt% Sr master alloy to the third alloy solution according to the composition ratio in Table 1 to obtain aluminum alloy melt. Under stirring conditions, hot-top casting is used to cast the aluminum alloy melt. The casting temperature is 740°C, the casting speed is 76mm / min, and the cooling water pressure is 0.07MPa. After the casting, an aluminum alloy with a diameter of 162mm is obtained. Alloy ingots and rods.
[0114] The ch
PUM
Property | Measurement | Unit |
---|---|---|
Diameter | aaaaa | aaaaa |
Diameter | aaaaa | aaaaa |
Thickness | aaaaa | aaaaa |
Abstract
Description
Claims
Application Information
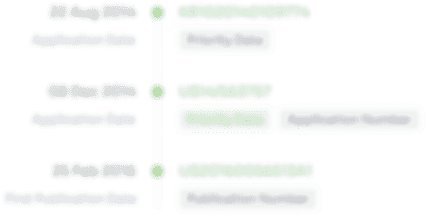
- R&D Engineer
- R&D Manager
- IP Professional
- Industry Leading Data Capabilities
- Powerful AI technology
- Patent DNA Extraction
Browse by: Latest US Patents, China's latest patents, Technical Efficacy Thesaurus, Application Domain, Technology Topic.
© 2024 PatSnap. All rights reserved.Legal|Privacy policy|Modern Slavery Act Transparency Statement|Sitemap