Preparation method of polyvinylidene fluoride resin
The technology of polyvinylidene fluoride resin and vinylidene fluoride is applied in the field of preparation of fluorine-containing polymers, which can solve the problems of long reaction time, residual dispersant, high production cost, and shorten the polymerization reaction time and post-treatment process. Simple, enhances the effect of reaction standing
- Summary
- Abstract
- Description
- Claims
- Application Information
AI Technical Summary
Benefits of technology
Problems solved by technology
Method used
Image
Examples
Embodiment 1
[0030] Add 3000mL of deionized water and 3g of paraffin to a 5L vertical stainless steel reactor, seal the reactor, and repeat the vacuum-filling process to remove O in the reactor. 2 , until the O in the kettle2 content is less than 20ppm, add 100g CF to the reaction kettle 2 ClCFCl 2 , 3g of diisopropyl peroxydicarbonate (IPP), 3g of ethyl acetate and 720g of VDF monomer (60% of the total amount of monomer). Control the stirring rate to 700r / min, raise the temperature to 75°C, and add 10mL of IPP-dissolved CF to the reactor every 60min since the reaction started. 2 ClCFCl 2 solution (5% concentration). And continuously add monomers to the kettle to keep the pressure in the reactor higher than 5.5MPa until all the 1200g monomers are added. Stop the reaction when the pressure in the kettle is less than 3.5MPa, and the whole reaction time is 5.5h. Recovering the remaining reaction monomers in the kettle, washing, drying and filtering the obtained product to obtain powdery P
Embodiment 2
[0040] After adding 3000 mL of deionized water and 2 g of paraffin into a 5 L vertical stainless steel reaction kettle, the reaction kettle was sealed. Repeat the vacuuming-nitrogen filling process several times to remove the O in the kettle 2 , until the O in the kettle 2 The content is less than 20ppm. Then add 230g of CF respectively in the reactor 2 ClCFCl 2 , 4g of di-n-propyl peroxydicarbonate, 5g of acetone and 1000g of VDF monomer. Control the stirring rate to 850r / min, raise the temperature to 80°C, and add 10mL of CF dissolved in di-n-propyl peroxydicarbonate to the reaction kettle every 50min since the reaction started. 2 ClCFCl 2 solution (5% concentration). Stop the reaction when the pressure in the kettle is less than 3MPa, and the whole reaction time is 3.5h. Recovering the remaining reaction monomers in the still, washing, drying and filtering the obtained product to obtain powdery PVDF resin. The test method is the same as in Example 1, and the product
Embodiment 3
[0042] Add 3000 mL of deionized water and 3 g of paraffin into a 5 L vertical stainless steel reaction kettle, and then seal the reaction kettle. Repeat the vacuuming-nitrogen filling process several times to remove the O in the kettle 2 , until the kettle O 2 The content is less than 20ppm. Then add 100g of CF to the reactor 2 ClCFCl 2 , 3g of diisobutyl peroxydicarbonate, 5g of ethyl acetate and 750g of VDF monomer (50% of the total amount of monomer). Control the stirring rate to 750r / min, and raise the temperature to 90°C. Add 3 mL of CF dissolved in diisobutyl peroxydicarbonate and ethyl acetate to the reaction kettle every 30 minutes since the start of the reaction. 2 ClCFCl 2 solution (wherein the concentration of diisobutyl peroxydicarbonate and ethyl acetate is 5%), and continuously add monomer in the kettle to keep the pressure in the reactor greater than 6MPa until all the addition of 1500g monomer is completed. Stop the reaction when the pressure in the kettl
PUM
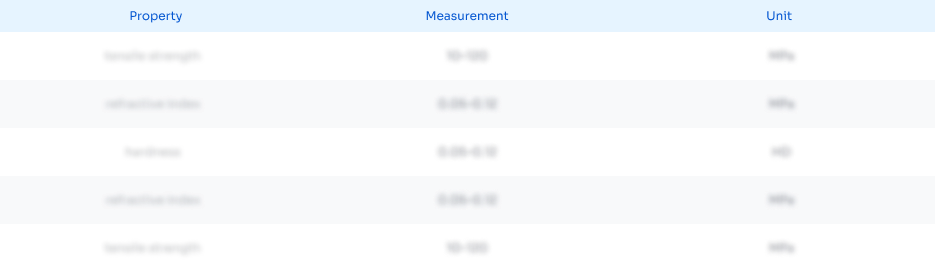
Abstract
Description
Claims
Application Information
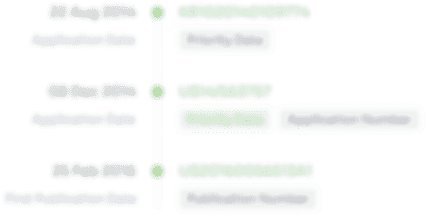
- R&D Engineer
- R&D Manager
- IP Professional
- Industry Leading Data Capabilities
- Powerful AI technology
- Patent DNA Extraction
Browse by: Latest US Patents, China's latest patents, Technical Efficacy Thesaurus, Application Domain, Technology Topic.
© 2024 PatSnap. All rights reserved.Legal|Privacy policy|Modern Slavery Act Transparency Statement|Sitemap