Super-fine grain twin-peak copper preparing method
A technology of ultra-fine grain and copper powder, applied in the direction of nanotechnology, can solve the problems of affecting material properties, low general toughness and ductility, unfavorable basic research work, etc., and achieve superior mechanical properties, high density, and simple process Effect
- Summary
- Abstract
- Description
- Claims
- Application Information
AI Technical Summary
Problems solved by technology
Method used
Image
Examples
Example Embodiment
[0016] Example 1:
[0017] A preparation method of ultra-fine crystal bimodal copper material includes the following steps:
[0018] Mixing: Use a TLHL three-dimensional blender to uniformly mix 70% by mass nanometer copper powder and 30% by mass micron copper powder for 20 minutes to obtain mixed copper powder;
[0019] Reduction: performing hydrogen reduction on the mixed copper powder in a high vacuum furnace for 30 minutes to 60 minutes to obtain reduced mixed copper powder, and the reaction temperature is set to 400°C to 500°C;
[0020] Cooling: cooling the reduced mixed copper powder to room temperature in an argon atmosphere;
[0021] High-temperature pressurization: the cooled reduced mixed copper powder is compressed at high temperature at 700°C, 800°C, and 900°C respectively; the pressure conditions of each compression process are all 5GPa; each compression process includes boosting 15 minutes, pressure maintaining for 30 minutes, and pressure reduction for 20 minutes; the press
Example Embodiment
[0030] Example 2:
[0031] A preparation method of ultra-fine crystal bimodal copper material includes the following steps:
[0032] Mixing: Use a TLHL three-dimensional mixer to uniformly mix 90% by mass nanometer copper powder and 10% by mass micron copper powder for 20 minutes to obtain mixed copper powder;
[0033] Reduction: performing hydrogen reduction on the mixed copper powder in a high vacuum furnace for 30 minutes to 60 minutes to obtain reduced mixed copper powder, and the reaction temperature is set to 400°C to 500°C;
[0034] Cooling: cooling the reduced mixed copper powder to room temperature in an argon atmosphere;
[0035] High-temperature reduction: the cooled reduced mixed copper powder is compressed at high temperatures at 700°C, 800°C, and 900°C; the pressure conditions of each compression process are all 5 GPa; each compression process includes a pressure increase 15 Minutes, pressure retention for 30 minutes, and pressure reduction for 20 minutes; the pressure reten
PUM
Property | Measurement | Unit |
---|---|---|
Tensile strength | aaaaa | aaaaa |
Tensile strength | aaaaa | aaaaa |
Tensile strength | aaaaa | aaaaa |
Abstract
Description
Claims
Application Information
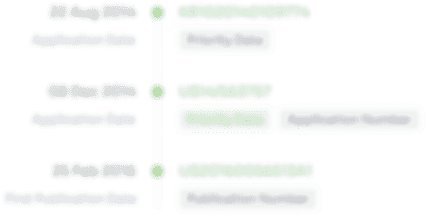
- R&D Engineer
- R&D Manager
- IP Professional
- Industry Leading Data Capabilities
- Powerful AI technology
- Patent DNA Extraction
Browse by: Latest US Patents, China's latest patents, Technical Efficacy Thesaurus, Application Domain, Technology Topic.
© 2024 PatSnap. All rights reserved.Legal|Privacy policy|Modern Slavery Act Transparency Statement|Sitemap