Ultra-low dielectric constant microwave dielectric ceramic EuY2V3O12 with low loss and high thermal stability
A microwave dielectric ceramic and ultra-low dielectric constant technology, applied in the field of dielectric ceramic materials, can solve the problems of few single-phase microwave dielectric ceramics, low quality factor, and excessive temperature coefficient of resonant frequency, so as to meet the requirements of low temperature co-firing. Technology, good temperature stability, low cost of raw materials
- Summary
- Abstract
- Description
- Claims
- Application Information
AI Technical Summary
Benefits of technology
Problems solved by technology
Method used
Image
Examples
Embodiment
[0018] Table 1 shows three specific examples of different sintering temperatures constituting the present invention and their microwave dielectric properties. The preparation method is as above, and the microwave dielectric performance is evaluated by the cylindrical dielectric resonator method; the phase analysis is carried out by X-ray diffraction analysis, and all samples are single-phase ceramics with a tetragonal zirconia structure.
[0019] The ceramics can be widely used in the manufacture of microwave devices such as various dielectric substrates, resonators and filters, and can meet the technical needs of mobile communication and satellite communication systems.
[0020] Table 1:
[0021]
PUM
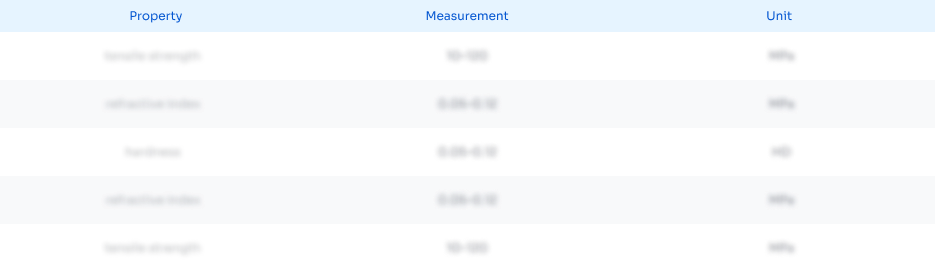
Abstract
Description
Claims
Application Information
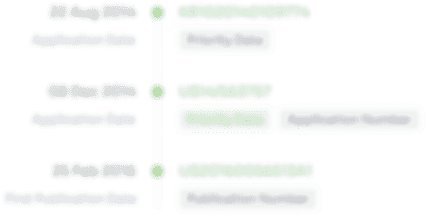
- R&D Engineer
- R&D Manager
- IP Professional
- Industry Leading Data Capabilities
- Powerful AI technology
- Patent DNA Extraction
Browse by: Latest US Patents, China's latest patents, Technical Efficacy Thesaurus, Application Domain, Technology Topic.
© 2024 PatSnap. All rights reserved.Legal|Privacy policy|Modern Slavery Act Transparency Statement|Sitemap