Pellet prepared through magnesium smelting waste
A magnesium smelting and pelletizing technology is applied in the field of pellets made from magnesium smelting waste residues and the field of preparation thereof, which can solve the problems of difficult recycling of metal smelting wastes and high manufacturing cost of pellets, so as to improve the purity and save raw materials. Cost, excellent results
- Summary
- Abstract
- Description
- Claims
- Application Information
AI Technical Summary
Problems solved by technology
Method used
Examples
Embodiment 1
[0016] The pellets of Example 1 were manufactured according to the following steps:
[0017] (1) Mix 100 grams of iron-containing dust, 0.5 grams of magnesium reduction slag powder (dicalcium silicate), 0.1 grams of magnesium refining slag (magnesium chloride) and 8 grams of Portland cement.
[0018] (2) Add 10 grams of water to each 100 grams of the mixture, and use a PanPelletizer to make pellets with a particle size of 25 mm.
[0019] (3) The pellets are dried, cured and cured.
[0020] The five pellet samples made according to the above steps were tested for compressive strength. The results are shown in Table 1.
[0021] Table 1 (Unit: Kg / piece)
[0022]
Embodiment 2
[0024] The pellets of Example 2 were manufactured according to the following steps:
[0025] (1) Mix 100 grams of iron ore powder, 1 grams of magnesium reduction slag powder (dicalcium silicate), 0.5 grams of magnesium refining slag (magnesium chloride) and 9 grams of Portland cement.
[0026] (2) Add 15 grams of water to each 100 grams of the mixture, and use a PanPelletizer to make pellets with a particle size of 22 mm.
[0027] (3) The pellets are dried, cured and cured.
[0028] The 5 pellet samples made according to the above steps were tested for compressive strength. The results are shown in Table 2.
[0029] Table 2 (Unit: Kg / piece)
[0030]
Embodiment 3
[0032] The pellets of Example 3 were manufactured according to the following steps:
[0033] (1) Refining 100 grams of iron dust sludge and iron ore powder mixture, the mass ratio of iron dust sludge to iron ore powder is 5:5, 3 grams of magnesium reduction slag powder (dicalcium silicate), 1 gram of magnesium The slag (magnesium chloride) and 10 grams of Portland cement are mixed evenly
[0034] (2) Add 20 grams of water to every 100 grams of the mixture, and make pellets with a particle size of 18 mm using a pan pelletizer.
[0035] (3) The pellets are dried, cured and cured.
[0036] The five pellet samples made according to the above steps were tested for compressive strength. The results are shown in Table 3.
[0037] Table 3 (Unit: Kg / piece)
[0038]
PUM
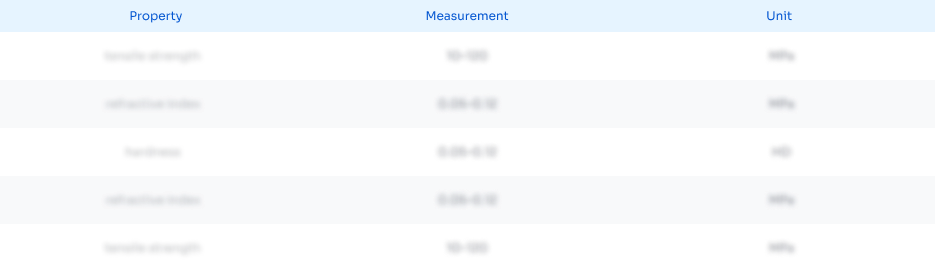
Abstract
Description
Claims
Application Information
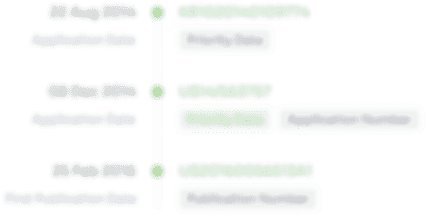
- R&D Engineer
- R&D Manager
- IP Professional
- Industry Leading Data Capabilities
- Powerful AI technology
- Patent DNA Extraction
Browse by: Latest US Patents, China's latest patents, Technical Efficacy Thesaurus, Application Domain, Technology Topic.
© 2024 PatSnap. All rights reserved.Legal|Privacy policy|Modern Slavery Act Transparency Statement|Sitemap