Process equipment for manufacturing aluminum alloy cable insulator and sheath
A technology of cable insulation and preparation process, which is applied in the direction of conductor/cable insulation, cable/conductor manufacturing, circuit, etc. It can solve the problems of high installation requirements, reversed and scratched wires, large wires, etc., and achieve smooth surface and good concentricity Effect
- Summary
- Abstract
- Description
- Claims
- Application Information
AI Technical Summary
Problems solved by technology
Method used
Image
Examples
Embodiment Construction
[0019] The present invention will be further described below in conjunction with accompanying drawing:
[0020] Such as figure 1 , figure 2 The shown one kind of aluminum alloy cable insulation and sheath preparation process equipment includes the inner mold 1, the middle mold 2 and the outer mold 3 which are fitted in sequence. The fitting here means that the rear part of the inner mold is located in the inner cavity of the middle mold The front part of the middle mold, the rear part of the middle mold is located in the inner cavity of the outer mold, the outer mold 3 is provided with a sheath shunt 4, the tail end of the outer mold 3 is provided with a die cover 5, and the outer wall of the inner mold 1 and the middle mold 2 A first annular passage 6 for injection of insulating material 100 is formed between the inner walls of the inner mold 2, a second annular passage 7 for injection of sheath material 200 is formed between the outer wall of the middle mold 2 and the inner w
PUM
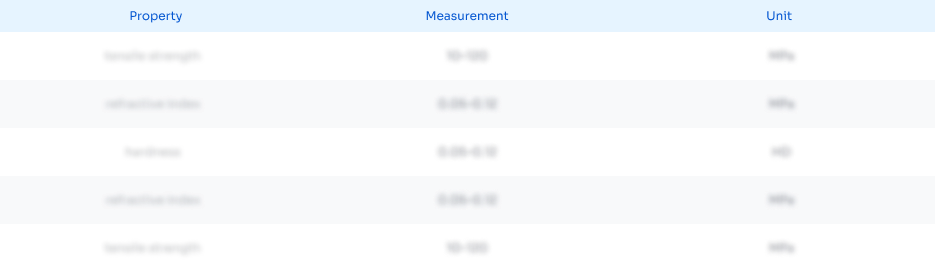
Abstract
Description
Claims
Application Information
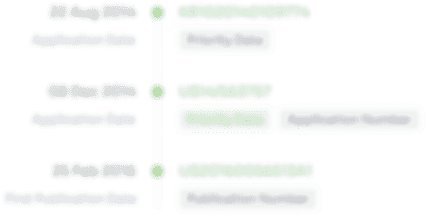
- R&D Engineer
- R&D Manager
- IP Professional
- Industry Leading Data Capabilities
- Powerful AI technology
- Patent DNA Extraction
Browse by: Latest US Patents, China's latest patents, Technical Efficacy Thesaurus, Application Domain, Technology Topic.
© 2024 PatSnap. All rights reserved.Legal|Privacy policy|Modern Slavery Act Transparency Statement|Sitemap