Color concrete and preparation method thereof
A colored concrete and cement technology, applied in the field of concrete, can solve the problems of affecting the service life of concrete, driver's visual fatigue, single color, etc., and achieve the effect of convenient batch and rapid production, simple production process and uniform color
- Summary
- Abstract
- Description
- Claims
- Application Information
AI Technical Summary
Benefits of technology
Problems solved by technology
Method used
Image
Examples
Embodiment 1
[0027] The ratio of raw materials is as follows: (unit: Kg / m 3 )
[0028]
[0029] Wherein: the above components meet the following indicators:
[0030] Cement: white Portland cement, whiteness not lower than grade two, the residue passing through a 0.8mm square hole sieve shall not exceed 10%, initial setting time ≥ 45min, final setting time ≤ 720min;
[0031] Through experiments, it is found that in the color cement process, the gray tone will weaken any color, making the color not pure and bright enough, and the gray tone cement will use a larger dose of pigment when preparing colored cement , which increases the preparation cost, so the present invention adopts white Portland cement with whiteness not lower than grade two;
[0032] Sand: medium sand in Zone II, mud content ≤ 3%;
[0033] Stone: crushed stone with a diameter of 5~16mm and a mud content of ≤2%;
[0034] Water: tap water or ground water;
[0035] Limestone mineral powder: white powder, 800 mesh, CaCO
Embodiment 2
[0052] The ratio of raw materials is as follows: (unit: Kg / m 3 )
[0053]
[0054] Wherein: the above components meet the following indicators:
[0055] Cement: white Portland cement, whiteness not lower than grade two, the residue passing through a 0.8mm square hole sieve shall not exceed 10%, initial setting time ≥ 45min, final setting time ≤ 720min;
[0056] Sand: medium sand in Zone II, mud content ≤ 3%;
[0057] Stone: crushed stone with a diameter of 5~16mm and a mud content of ≤2%;
[0058] Water: tap water or ground water;
[0059] Limestone mineral powder: white powder, 800 mesh, CaCO 3 Content ≥ 70 (%), magnesium content ≤ 34 (%), iron content ≤ 11 (%);
[0060] White carbon black: content 98-99.9%, 2000-8000 mesh;
[0061] Admixture: polycarboxylate high-performance water reducer, concentration 20%, water reducing rate ≥ 25%;
[0062] Pigment: blue pigment cobalt oxide, green powder, oil absorption: 16-20g / 100g, density: 4.01-5.01g / cm 3 , PH value: 7-9;
Embodiment 3
[0075] The ratio of raw materials is as follows: (unit: Kg / m 3 )
[0076]
[0077] Wherein: the above components meet the following indicators:
[0078] Cement: white Portland cement, whiteness not lower than grade two, the residue passing through a 0.8mm square hole sieve shall not exceed 10%, initial setting time ≥ 45min, final setting time ≤ 720min;
[0079] Sand: medium sand in Zone II, mud content ≤ 3%;
[0080] Stone: crushed stone with a diameter of 5~16mm and a mud content of ≤2%;
[0081] Water: tap water or ground water;
[0082] Limestone mineral powder: white powder, 800 mesh, CaCO3 content ≥ 70 (%), magnesium content ≤ 34 (%), iron content ≤ 11 (%);
[0083] White carbon black: content 98-99.9%, 2000-8000 mesh;
[0084] Admixture: polycarboxylate high-performance water reducer, concentration 20%, water reducing rate ≥ 25%;
[0085] Pigment: light yellow pigment iron oxide yellow, Fe2O3 content ≥ 86%, moisture 1.0 ≤%, oil absorption 25~35 (ml / 100g), pH va
PUM
Property | Measurement | Unit |
---|---|---|
Diameter | aaaaa | aaaaa |
Oil absorption | aaaaa | aaaaa |
Slump | aaaaa | aaaaa |
Abstract
Description
Claims
Application Information
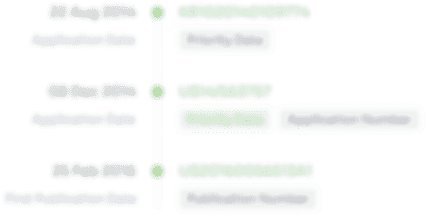
- R&D Engineer
- R&D Manager
- IP Professional
- Industry Leading Data Capabilities
- Powerful AI technology
- Patent DNA Extraction
Browse by: Latest US Patents, China's latest patents, Technical Efficacy Thesaurus, Application Domain, Technology Topic.
© 2024 PatSnap. All rights reserved.Legal|Privacy policy|Modern Slavery Act Transparency Statement|Sitemap