Super-hydrophobic coating containing candle soot and preparation method of same
A technology of super-hydrophobic coating and hydrophobic coating, applied in the application field, can solve the problems of harsh preparation conditions, unsuitable for industrial production, cumbersome steps, etc., and achieve the effects of wide range of uses, simple method and good adhesion
- Summary
- Abstract
- Description
- Claims
- Application Information
AI Technical Summary
Problems solved by technology
Method used
Image
Examples
Example Embodiment
[0023] Example 1
[0024] Preparation of a super-hydrophobic coating containing candle soot:
[0025] S1. The deposition of candle soot on the surface of the glass substrate: After the glass slide (rectangular, 7.6cm*2.6cm) is washed and dried, the surface that needs to be prepared with a hydrophobic coating covers 1 / 3 to 1 of the burning candle / 2 flame and move the glass slide until the surface where the hydrophobic coating needs to be prepared is evenly covered with a layer of candle soot, and the thickness of this layer of candle soot is about 2 μm;
[0026] S2. Preparation of super-hydrophobic coating by vapor deposition: Put the glass slide covered with candle soot prepared in S1 into a cylindrical crucible (diameter 10cm, height 2cm), and add 0.15mL to the crucible (0.44mmol) liquid perfluorodecyltrichlorosilane, heated to 224°C to completely transform the liquid perfluorodecyltrichlorosilane into gaseous state, the concentration of gaseous perfluorodecyltrichlorosilane in a
Example Embodiment
[0027] Example 2
[0028] Preparation of a super-hydrophobic coating containing candle soot:
[0029] S1. The deposition of candle soot on the surface of the glass substrate: After the glass slide (rectangular, 7.6cm*2.6cm) is washed and dried, the surface that needs to be prepared with a hydrophobic coating covers 1 / 3 to 1 of the burning candle / 2 flame and move the glass slide until the surface where the hydrophobic coating needs to be prepared is evenly covered with a layer of candle soot, the thickness of this layer of candle soot is about 3.5 μm; figure 1 Is the scanning electron microscope image of the candle soot deposited on the glass slide. figure 1 It can be seen that the candle soot forms a nano-sized rough structure on the surface of the glass slide.
[0030] S2. Preparation of super-hydrophobic coating by vapor deposition: Put the glass slide covered with candle soot prepared in S1 into a cylindrical crucible (diameter 10cm, height 2cm), and add 0.3mL to the crucible (
Example Embodiment
[0031] Example 3
[0032] Preparation of a super-hydrophobic coating containing candle soot:
[0033] S1. The deposition of candle soot on the surface of the glass substrate: After the glass slide (rectangular, 7.6cm*2.6cm) is washed and dried, the surface that needs to be prepared with a hydrophobic coating covers 1 / 3 to 1 of the burning candle / 2 flame and move the glass slide until the surface where the hydrophobic coating needs to be prepared is evenly covered with a layer of candle soot, the thickness of this layer of candle soot is about 5 μm;
[0034] S2. Preparation of super-hydrophobic coating by vapor deposition: Put the glass slide covered with candle soot prepared in S1 into a cylindrical crucible (diameter 10cm, height 2cm), and add 0.5 mL to the crucible (1.47mmol) Liquid perfluorodecyltrichlorosilane, heated to 230°C to completely transform the liquid perfluorodecyltrichlorosilane into gaseous state, the concentration of gaseous perfluorodecyltrichlorosilane in a clo
PUM
Property | Measurement | Unit |
---|---|---|
Thickness | aaaaa | aaaaa |
Thickness | aaaaa | aaaaa |
Thickness | aaaaa | aaaaa |
Abstract
Description
Claims
Application Information
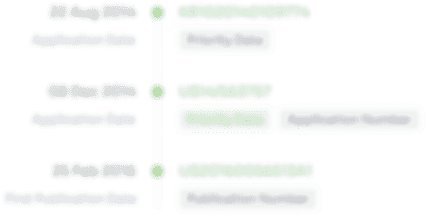
- R&D Engineer
- R&D Manager
- IP Professional
- Industry Leading Data Capabilities
- Powerful AI technology
- Patent DNA Extraction
Browse by: Latest US Patents, China's latest patents, Technical Efficacy Thesaurus, Application Domain, Technology Topic.
© 2024 PatSnap. All rights reserved.Legal|Privacy policy|Modern Slavery Act Transparency Statement|Sitemap