Production technology of ultra-large-pore adsorptive silica gels
A production process and ultra-large pore technology, applied in the direction of silicon oxide, silicon dioxide, etc., can solve problems such as ineffective effects, and achieve the effects of improving device utilization, shortening production cycle, and uniform particle size distribution
- Summary
- Abstract
- Description
- Claims
- Application Information
AI Technical Summary
Problems solved by technology
Method used
Examples
Example Embodiment
[0016] Implementation example 1:
[0017] First add 10 liters of 15% sulfuric acid solution into the experimental reaction tower, and then add 6 liters of prepared SiO 2 Sodium silicate solution with a content of 30% was sprayed into the experimental reaction tower. The temperature in the tower was 105℃. After aging for 16 hours in an acidic solution with a pH value of 1-3, it entered the experimental water-washing tank. Wash in water at ℃, and after washing for 70 hours, carry out ammonia soaking for 7 hours, and then the temperature of the oven in the filter press drying stage is 100 ℃, and the drying time is 50 hours. The experimental data are shown in Table 1.
[0018] Table 1 Experimental data table
[0019]
Example Embodiment
[0020] Implementation example 2:
[0021] First add 10 liters of 18% sulfuric acid solution to the experimental reaction tower, and then add 6 liters of prepared SiO 2 Sodium silicate solution with a content of 35% was sprayed into the experimental reaction tower at a temperature of 107°C. After aging for 17 hours in an acidic solution with a pH value of 1-3, it enters the experimental water-washing tank. Wash in water at ℃, and after 72 hours of washing, carry out ammonia soaking for 7 hours, and then the temperature of the oven in the filter drying stage is 130℃, and the drying time is 52 hours. The experimental data are shown in Table 2.
[0022] Table 2 Experimental data table
[0023]
Example Embodiment
[0024] Implementation example 3:
[0025] First add 10 liters of 20% sulfuric acid solution to the experimental reaction tower, and then add 6 liters of prepared SiO 2 The sodium silicate solution with a content of 38% was sprayed into the experimental reaction tower. The temperature in the tower was 109℃. After aging for 15 hours in an acidic solution with a pH value of 1-3, it entered the experimental water-washing tank. Wash in water at ℃, and after washing for 73 hours, carry out ammonia soaking for 7 hours. Then, the temperature of the oven in the filter drying stage is 140℃, and the drying time is 50 hours. The experimental data are shown in Table 3.
[0026] Table 3 Experimental data table
[0027]
PUM
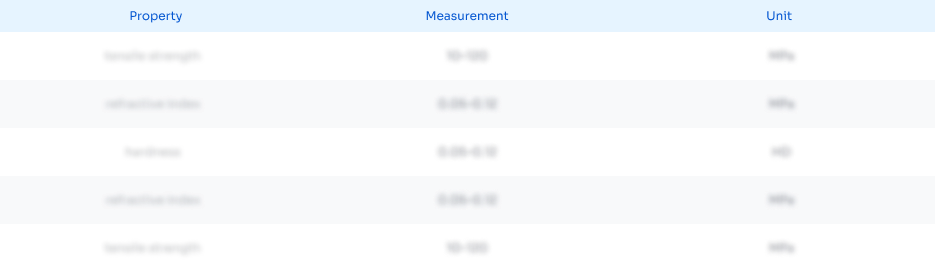
Abstract
Description
Claims
Application Information
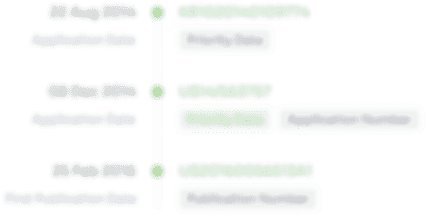
- R&D Engineer
- R&D Manager
- IP Professional
- Industry Leading Data Capabilities
- Powerful AI technology
- Patent DNA Extraction
Browse by: Latest US Patents, China's latest patents, Technical Efficacy Thesaurus, Application Domain, Technology Topic.
© 2024 PatSnap. All rights reserved.Legal|Privacy policy|Modern Slavery Act Transparency Statement|Sitemap