Preparation method of high-temperature graphite anode material for lithium-ion battery
A lithium-ion battery and graphite negative electrode technology, which is applied to battery electrodes, secondary batteries, circuits, etc., can solve problems such as inability to use, battery flatulence, etc., achieve less production equipment, reduce battery polarization and internal resistance, and electrochemical Stability and security performance improvements
- Summary
- Abstract
- Description
- Claims
- Application Information
AI Technical Summary
Benefits of technology
Problems solved by technology
Method used
Image
Examples
Embodiment 1
[0015] A method for preparing a graphite negative electrode material for a high-temperature lithium-ion battery. First, weigh graphite, a solvent, and ammonia water in a ratio of 1g:0.5L:2mL, add them to a high-speed mixer, and disperse them for 1 hour at a speed of 500r / min to obtain a mixed mixture. Then, add titanate drop by drop, the ratio of the mixed slurry to titanate is 1g:2mL; then, after adding titanate, react in a water bath at 80°C for 5h, after the reaction is completed, wash with water and ethanol repeatedly 4 times, finally, dry in a drying oven at 80°C, put it in an atmosphere protection furnace for sintering after drying, raise the temperature to 400°C at a rate of 2°C / min and keep it for 18 hours to obtain a high-temperature lithium-ion battery Graphite anode material.
[0016] The graphite is natural graphite, the purity is above 99.999, and the particle size d50=10-20um.
[0017] The solvent is at least one of ethanol, propanol and butanol, and the purity
Embodiment 2
[0022] A preparation method of high-temperature lithium-ion battery graphite negative electrode material. First, weigh graphite, solvent, and ammonia water in a ratio of 1g:2L:10mL, add them to a high-speed mixer, and disperse them at a speed of 2000r / min for 0.5h to obtain a mixture. Then, add titanate drop by drop, the ratio of the mixed slurry to titanate is 1g:5mL; then, after adding titanate, react in a water bath at 80°C for 5h, and wash with water and ethanol repeatedly after the reaction is completed 4 times, finally, dry it in a drying oven at 100°C, put it in an atmosphere protection furnace for sintering after drying, raise the temperature to 800°C at a rate of 25°C / min and hold it for 4 hours to obtain a high-temperature lithium-ion battery Graphite anode material.
[0023] The graphite is natural graphite, the purity is above 99.999, and the particle size d50=10-20um.
[0024] The solvent is at least one of ethanol, propanol and butanol, and the purity is above
Embodiment 3
[0029] A method for preparing a high-temperature lithium-ion battery graphite negative electrode material. First, weigh graphite, solvent, and ammonia water in a ratio of 1g:1L:6mL, add them to a high-speed mixer, and disperse them at a speed of 1000r / min for 0.7h to obtain a mixture. Then, add titanate drop by drop, the ratio of the mixed slurry to titanate is 1g:3mL; then, after adding titanate, react in a water bath at 50°C for 60h, after the reaction is completed, wash with water and ethanol repeatedly 4 times, finally, dry it in a drying oven at 100°C, place it in an atmosphere protection furnace for sintering after drying, raise the temperature to 600°C at a rate of 15°C / min and hold it for 8 hours to obtain a high-temperature lithium-ion battery Graphite anode material.
[0030] The graphite is natural graphite, the purity is above 99.999, and the particle size d50=10-20um.
[0031] The solvent is at least one of ethanol, propanol and butanol, and the purity is above
PUM
Property | Measurement | Unit |
---|---|---|
Granularity | aaaaa | aaaaa |
Abstract
Description
Claims
Application Information
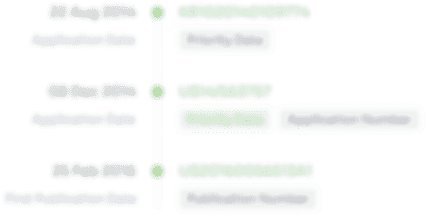
- R&D Engineer
- R&D Manager
- IP Professional
- Industry Leading Data Capabilities
- Powerful AI technology
- Patent DNA Extraction
Browse by: Latest US Patents, China's latest patents, Technical Efficacy Thesaurus, Application Domain, Technology Topic.
© 2024 PatSnap. All rights reserved.Legal|Privacy policy|Modern Slavery Act Transparency Statement|Sitemap