Two-bath dyeing method for superfine fiber synthetic leather
A technology of superfine fiber and dyeing method, which is applied in the field of dyeing process of synthetic leather, which can solve the problems of not being able to meet the high-end market, dyes are easy to fall off, and dry and wet rubbing fastness is low.
- Summary
- Abstract
- Description
- Claims
- Application Information
AI Technical Summary
Problems solved by technology
Method used
Examples
Embodiment 1
[0029] (1) Pretreatment process
[0030] Put the superfine fiber synthetic leather into the high temperature and high pressure overflow dyeing machine, add 6g / L scouring agent, the bath ratio is 1:10, the temperature is 70°C, and the liquid is drained after scouring for 30 minutes.
[0031] The scouring agent in the step (1) is a commercial product, the scouring agent DM-1324 of Demei Chemical.
[0032] (2) dyeing process
[0033] Sulfur dye dyeing: add sulfur dye 3% (o.w.f.) and caustic soda 1g / L at room temperature, liquor ratio 1:5, run for 15 minutes and then heat up, 1°C / min to 60°C, then add hydrosulfite 5g / L and caustic soda 1g / L The mixture was kept warm for 30min, drained and washed with 0.1g / L acetic acid and 1.5g / L H 2 o 2 (35%) Oxidation at 50°C for 30min, then soaping agent SN-S 0.5g / L, soaping at 90°C for 30min to drain.
[0034] Acid dye dyeing: Add 1% (o.w.f.) acid dye at room temperature, 1% (o.w.f.) leveling agent, 0.5g / L acetic acid, 0.1g
Embodiment 2
[0041] (1) Pretreatment process
[0042] Put the superfine fiber synthetic leather into the high temperature and high pressure overflow dyeing machine, add 9g / L scouring agent, the bath ratio is 1:40, the temperature is 80°C, and the liquid is drained after scouring for 60 minutes.
[0043] The scouring agent is DM-1324 from Demei Chemical.
[0044] (2) dyeing process
[0045] Sulfur dye dyeing: add sulfur dye 8% (o.w.f.) and caustic soda 3g / L at room temperature, bath ratio 1:15, run for 20 minutes and then heat up, 3°C / min to 85°C, then add hydrosulfite 15g / L and caustic soda 2g / L The mixture was kept warm for 60min, drained and washed with 1g / L acetic acid and 3.5g / L H 2 o 2 (35%) Oxidation at 70°C for 60min, then soaping agent SN-S 2g / L, soaping at 100°C for 60min to drain.
[0046] Acid dye dyeing: add acid dye 5% (o.w.f.) at room temperature, leveling agent dosage is 3% (o.w.f.), acetic acid dosage is 2g / L, defoamer dosage is 0.5g / L, bath ratio 1:15,
Embodiment 3
[0053] (1) Pretreatment process
[0054] Put the superfine fiber synthetic leather into the high temperature and high pressure overflow dyeing machine, add 8g / L scouring agent, the bath ratio is 1:20, the temperature is 75°C, and the liquid is drained after scouring for 45 minutes.
[0055] The scouring agent is DM-1324 from Demei Chemical.
[0056] (2) dyeing process
[0057]Sulfur dye dyeing: Add sulfur dye 6% (o.w.f.) and caustic soda 2g / L at room temperature, liquor ratio 1:10, run for 18 minutes and then heat up, 2°C / min to 70°C, then add hydrosulfite 10g / L and caustic soda 1.5g / L of mixed solution, keep warm for 50min, wash with 0.5g / L acetic acid and 2g / L H 2 o 2 (35%) Oxidation at 60°C for 45min, then soaping agent SN-S 1g / L, soaping at 95°C for 45min to drain.
[0058] Acid dye dyeing: Add acid dye 3% (o.w.f.) at room temperature, leveling agent dosage 2% (o.w.f.), acetic acid dosage 1g / L, defoamer dosage 0.3g / L, bath ratio 1:10, 100℃ After heat
PUM
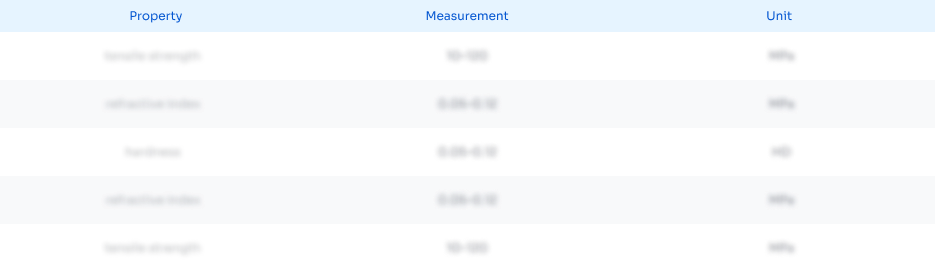
Abstract
Description
Claims
Application Information
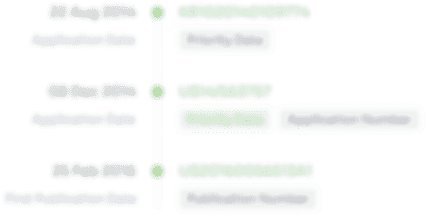
- R&D Engineer
- R&D Manager
- IP Professional
- Industry Leading Data Capabilities
- Powerful AI technology
- Patent DNA Extraction
Browse by: Latest US Patents, China's latest patents, Technical Efficacy Thesaurus, Application Domain, Technology Topic.
© 2024 PatSnap. All rights reserved.Legal|Privacy policy|Modern Slavery Act Transparency Statement|Sitemap