Extraction method
A technology of extraction and saponification agent, applied in the field of extraction, can solve problems such as reducing product quality, and achieve the effects of improving product quality, low temperature and convenient use
- Summary
- Abstract
- Description
- Claims
- Application Information
AI Technical Summary
Benefits of technology
Problems solved by technology
Method used
Image
Examples
Embodiment 1
[0087] The blank organic phase that extractant is P204:P507=1 (volume) is saponified with the suspension liquid preparation of commercially available calcium carbonate (containing about 2% of magnesium carbonate) described in the following table one, obtains calcium saponification organic phase and saponification wastewater (discarded) go). The calcium saponified organic phase is fully mixed with the neodymium acetate solution to obtain a mixed solution of magnesium acetate and calcium acetate and a loaded organic phase. The loaded organic phase was back-extracted with 5N hydrochloric acid (AR) to obtain neodymium chloride solution 1 and a blank organic phase.
[0088] In the process of preparing the calcium saponification organic phase, easily extracted impurity elements such as iron in commercially available calcium carbonate relative to the calcium element enter the blank organic phase together with the calcium element and become part of the saponification organic phase; while
Embodiment 2
[0103] see figure 1 . In the first stage of the praseodymium-neodymium extraction and separation production line, add the blank organic phase that the extraction agent is P507, and then add the suspension of domestic magnesium oxide (see the following table 3 for details, in which the heavy metal elements are calculated as PbO, the same below) and water as described in Table 3. liquid to obtain magnesium saponified organic phase (organic phase loaded with magnesium) and saponified residual liquid (abandoned); the mixed solution of magnesium saponified organic phase and praseodymium chloride and neodymium chloride (see Table 5 for details, wherein Pr 6 o 11 22wt%, Nd 2 o 3 78wt%; the elements to be separated and the separated elements are calculated as oxides, the same below) are separated by countercurrent extraction and separation in multistage mixing and settling tanks, and washed with industrial hydrochloric acid and back-extracted to obtain magnesium chloride solution 1 an
Embodiment 3
[0125] Carbide slag (relevant parameters are shown in Table 6 below, wherein a small amount of magnesium is calculated as calcium element) is dissolved in ammonium nitrate solution and filtered to make saponified solution 1.
[0126] Mix an appropriate amount of saponification solution 1 with a blank organic phase whose extractant is P507 at a volume ratio of 1:1 to obtain calcium saponification organic phase and ammonium nitrate solution 1; 6) Mix and separate the calcium nitrate solution 1, use 5N nitric acid according to the volume ratio of nitric acid:loaded organic phase = 1:1 back extraction, lanthanum nitrate solution 1 (see Table 7 for related parameters) and blank organic phase. Calcium oxide is prepared by concentrating and crystallizing calcium nitrate solution and then roasting.
[0127] Calcium oxide 1 is digested to become regenerated calcium hydroxide (relevant parameters are shown in Table 7) and then saponification solution 2 is prepared with ammonium nitrate sol
PUM
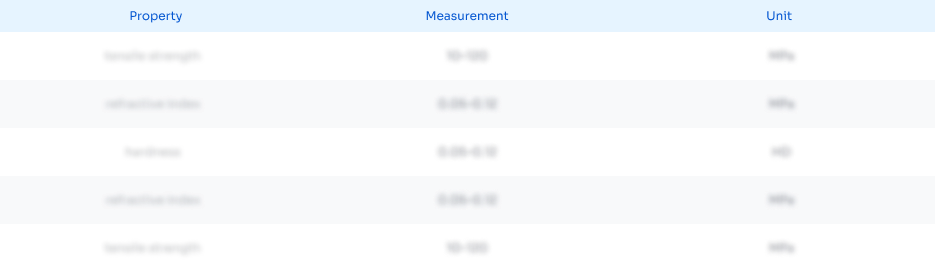
Abstract
Description
Claims
Application Information
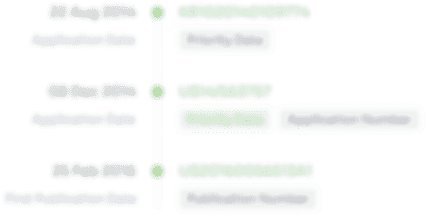
- R&D Engineer
- R&D Manager
- IP Professional
- Industry Leading Data Capabilities
- Powerful AI technology
- Patent DNA Extraction
Browse by: Latest US Patents, China's latest patents, Technical Efficacy Thesaurus, Application Domain, Technology Topic.
© 2024 PatSnap. All rights reserved.Legal|Privacy policy|Modern Slavery Act Transparency Statement|Sitemap