Resin catalyst for synthesis and preparation of ethylene glycol tertiary butyl ether and modification method thereof
A technology of ethylene glycol tert-butyl ether and catalyst, which is applied in the fields of chemical instruments and methods, organic compound/hydride/coordination complex catalyst, catalyst activation/preparation, etc. Low, poor catalytic activity and other problems, to achieve the effect of improving catalytic activity and selectivity, high conversion rate and selectivity, and improving strength
- Summary
- Abstract
- Description
- Claims
- Application Information
AI Technical Summary
Benefits of technology
Problems solved by technology
Method used
Image
Examples
Embodiment 1
[0013] Modified catalyst C-1:
[0014] ①. Modification treatment: Add 200ml of acetone to a stainless steel stirred kettle with a reflux condensing device, and then add 50g of dry polystyrene hydrogen cationic resin catalyst into the kettle. After the temperature rises to 40°C, hydrogen chloride gas is introduced into the kettle to make the pressure inside the kettle 0.2MPa, the temperature is raised to 80°C, and the reaction is stirred for 10 hours, and then the liquid is filtered off; the dry polystyrene hydrogen cationic resin catalyst , obtained by drying in an oven at 80°C for 6 hours, and then cooling naturally;
[0015] ②, purification treatment:
[0016] Put the modified resin catalyst in step ① in deionized water at 80°C, boil under reduced pressure at -0.090MPa for 6 hours, wash twice with deionized water, and dry at room temperature to obtain. Get above-mentioned freshly modified resin catalyst 50ml and pack in the fixed-bed reactor of internal diameter 10mm, length
Embodiment 2
[0018] Modified catalyst C-2:
[0019] ①. Modification treatment:
[0020] In the stainless steel stirred tank with reflux condensing device, add acetone 200ml, then drop into dry polystyrene hydrogen cationic resin catalyst 50g in the still. After the temperature rises to 50°C, hydrogen chloride gas is introduced into the kettle to make the pressure in the kettle 0.2 MPa, the temperature is raised to 80°C, and the reaction is stirred for 8 hours, and then the liquid is filtered off; the dry polystyrene hydrogen cationic resin catalyst , obtained by drying in an oven at 100°C for 4 hours, and then cooling naturally;
[0021] ②, purification treatment:
[0022] The resin catalyst modified in step ① was placed in deionized water at 85°C, boiled under reduced pressure for 6 hours under a pressure of -0.095MPa, washed twice with deionized water, and dried at room temperature to obtain.
[0023] Get above-mentioned freshly modified resin catalyst 50ml and pack in the fixed-bed reac
Embodiment 3
[0025] Modified catalyst C-3:
[0026] ①. Modification treatment: Add 200ml of acetone to a stainless steel stirred kettle with a reflux condensing device, and then put 70g of dry polystyrene hydrogen-type cationic resin catalyst into the kettle. After the temperature rises to 50°C, hydrogen chloride gas is introduced into the kettle to make the pressure inside the kettle 0.5MPa, the temperature is raised to 75°C, and the reaction is stirred for 8 hours, and then the liquid is filtered off; the dry polystyrene hydrogen cationic resin catalyst , obtained by drying in an oven at 120°C for 4 hours, and then cooling naturally;
[0027] ②, purification treatment:
[0028] Put the modified resin catalyst in step ① in deionized water at 80°C, boil under reduced pressure at -0.090MPa for 3 hours, wash twice with deionized water, and dry at room temperature to obtain.
[0029] Get above-mentioned freshly modified resin catalyst 50ml and pack in the fixed-bed reactor of internal diameter
PUM
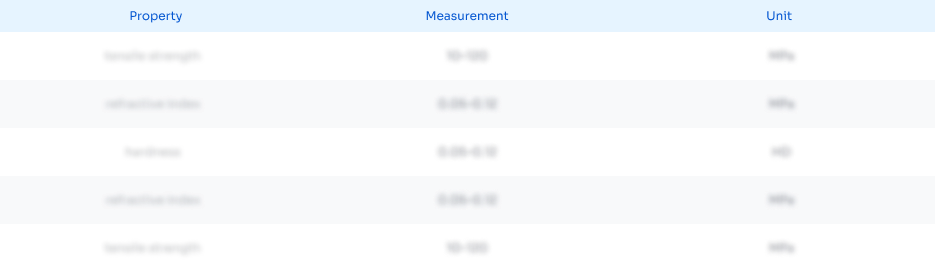
Abstract
Description
Claims
Application Information
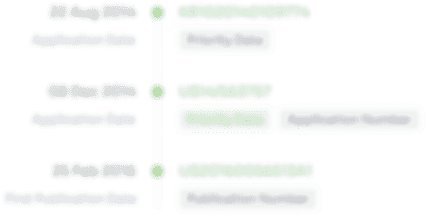
- R&D Engineer
- R&D Manager
- IP Professional
- Industry Leading Data Capabilities
- Powerful AI technology
- Patent DNA Extraction
Browse by: Latest US Patents, China's latest patents, Technical Efficacy Thesaurus, Application Domain, Technology Topic.
© 2024 PatSnap. All rights reserved.Legal|Privacy policy|Modern Slavery Act Transparency Statement|Sitemap