Preparation method of solar cell back film
A solar cell and back film technology, which is applied in the field of solar cell back film preparation, can solve problems such as high shrinkage rate of the back film, influence on photoelectric conversion and appearance, and deformation of the back film, so as to reduce thermal shrinkage rate, prevent deformation, and improve The effect of shrinkage strength
- Summary
- Abstract
- Description
- Claims
- Application Information
AI Technical Summary
Problems solved by technology
Method used
Image
Examples
Example Embodiment
[0019] Example 1
[0020] First, weigh 30 parts of deionized water, 8 parts of ethyl orthosilicate, 90 parts of absolute ethanol and 2 parts of 5% hydrochloric acid by weight in parts by weight and place them in a beaker. After stirring and mixing evenly, place the beaker Heat in a water bath at 50℃ for 2h, after the water bath is heated, let it stand and cool to room temperature to obtain a silica sol, and then weigh 50 parts by weight of 15% acetic acid solution and 15 parts by weight respectively. Sodium benzene sulfonate and 5 parts of methyltrimethoxysilane were placed in a beaker, heated in a water bath at 50°C for 3 hours, and then allowed to stand and cool to room temperature to prepare a modified gel solution; according to the volume ratio of 1:2, the modified gel was prepared. The mixed gel liquid was stirred and mixed with silica sol and placed under 300W ultrasonic dispersion treatment for 20 minutes to obtain a mixed gel liquid. The mixed gel liquid was vacuum freeze-dr
Example Embodiment
[0021] Example 2
[0022] First, weigh 25 parts of deionized water, 5 parts of ethyl orthosilicate, 85 parts of absolute ethanol, and 1 part of 5% hydrochloric acid by weight in parts by weight, put them in a beaker, stir and mix evenly, then place the beaker Heated in a water bath at 45℃ for 1h. After the water bath is heated, let it stand and cool to room temperature to obtain a silica sol. Then, in parts by weight, weigh 45 parts by weight of 15% acetic acid solution and 10 parts of dodecane. Sodium benzene sulfonate and 3 parts of methyltrimethoxysilane were placed in a beaker, heated in a water bath at 45°C for 2 hours, and then allowed to stand and cool to room temperature to prepare a modified gel solution; according to the volume ratio of 1:2, the modified gel The mixed gel liquid was stirred and mixed with the silica sol and placed under 200W ultrasonic dispersion treatment for 15 minutes to obtain a mixed gel liquid. The mixed gel liquid was vacuum freeze-dried and placed
Example Embodiment
[0023] Example 3
[0024] First, weigh 27 parts of deionized water, 6 parts of ethyl orthosilicate, 87 parts of absolute ethanol and 2 parts of 5% hydrochloric acid by weight in parts by weight and place them in a beaker. After stirring and mixing, place the beaker Heat in a water bath at 47°C for 2 hours. After the water bath is heated, let it stand and cool to room temperature to obtain silica sol. Then, by weight, weigh 47 parts of 15% acetic acid solution and 12 parts of dodecane. Sodium benzene sulfonate and 4 parts of methyltrimethoxysilane were placed in a beaker, heated in a water bath at 47°C for 2h, then stood and cooled to room temperature to prepare a modified gel solution; according to the volume ratio of 1:2, change The mixed gel liquid was stirred and mixed with the silica sol and placed under 250W ultrasonic dispersion treatment for 17 minutes to obtain a mixed gel liquid. The mixed gel liquid was vacuum freeze-dried and placed in a ball mill tank, and ball milled at
PUM
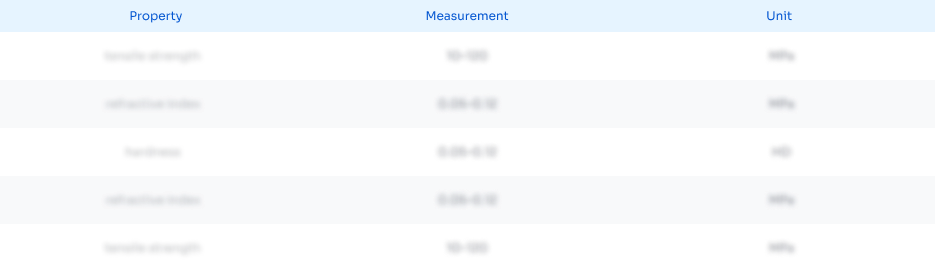
Abstract
Description
Claims
Application Information
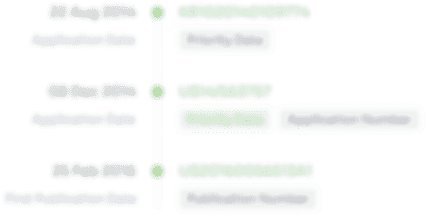
- R&D Engineer
- R&D Manager
- IP Professional
- Industry Leading Data Capabilities
- Powerful AI technology
- Patent DNA Extraction
Browse by: Latest US Patents, China's latest patents, Technical Efficacy Thesaurus, Application Domain, Technology Topic.
© 2024 PatSnap. All rights reserved.Legal|Privacy policy|Modern Slavery Act Transparency Statement|Sitemap