Stirring production line
A production line and mixing device technology, which is applied to cement mixing devices, batching weighing instruments, and raw material supply devices for sale, etc., can solve the problems of reducing processing efficiency, time-consuming and laborious, and low efficiency, so as to reduce equipment costs and avoid easy knots. The scab, the effect of the simple structure of the device
- Summary
- Abstract
- Description
- Claims
- Application Information
AI Technical Summary
Problems solved by technology
Method used
Image
Examples
Example Embodiment
[0016] refer to figure 1 , A stirring production line of the present invention includes a feed bin 1, the upper part of the feed bin 1 is longitudinally provided with a separator 2, and the separator 2 divides the feed bin 1 into an aggregate bin 11 and a powder bin 11. The silo 12, the lower part of the feeding silo 1 is provided with a mixing cavity 13, the mixing cavity 13 is connected with the aggregate silo 11 and the powder silo 12, and a stirring device 4 is arranged below the mixing cavity 13 . When in use, lime and other powders enter from the powder silo 12, and aggregates such as stone particles enter from the aggregate silo 11. After being mixed in the mixing chamber 13, they are discharged from the outlet of the mixing chamber 13. Since the stirring device 4 is relatively wet, Therefore, the powder is easy to scab, but the setting of the separator 2 and the mixing chamber 13, even if the powder is partially scabbed due to moisture, it will be hit by the aggregates s
PUM
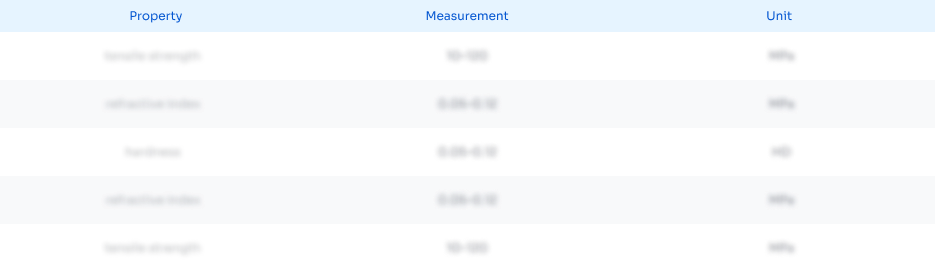
Abstract
Description
Claims
Application Information
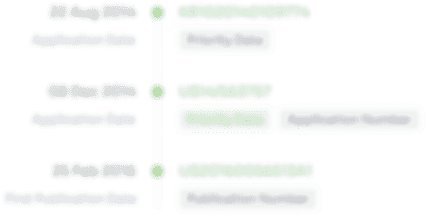
- R&D Engineer
- R&D Manager
- IP Professional
- Industry Leading Data Capabilities
- Powerful AI technology
- Patent DNA Extraction
Browse by: Latest US Patents, China's latest patents, Technical Efficacy Thesaurus, Application Domain, Technology Topic.
© 2024 PatSnap. All rights reserved.Legal|Privacy policy|Modern Slavery Act Transparency Statement|Sitemap