Zr and Ba-containing zinc alloy for hot dip galvanizing of aluminum alloys at low temperature
A hot-dip galvanizing and aluminum alloy technology, applied in the field of alloys, can solve the problems of development cycle, design quality, process quality is difficult to guarantee, and enterprises cannot obtain greater breakthroughs, and achieve the effect of hindering oxidation and volatilization.
- Summary
- Abstract
- Description
- Claims
- Application Information
AI Technical Summary
Benefits of technology
Problems solved by technology
Method used
Examples
Embodiment 1
[0018] Zinc alloys containing Zr and Ba for hot-dip galvanizing of aluminum alloys at low temperatures. In terms of weight percentage, the chemical composition of the material is: Ba: 0.8wt.%, Zr: 0.5wt.%, In: 0.4wt.%, Mn: 1.5wt.%, V: 0.4wt.%, Bi: 1.5 wt.%, the balance is zinc. Preparation method: Add the above-mentioned raw materials into the atmosphere-protected induction furnace, and use a silicon carbide crucible; induction heat to 550 degrees to form an alloy solution, and use the electromagnetic stirring effect to fully stir for about 10 minutes; put the alloy liquid at 550 degrees After heat preservation and standing for 10 minutes, it is cast into the equipment at the same level as the hot top for semi-continuous casting into required round ingots, and the ingot moving speed is 14m / min. The ingot can be used as a zinc alloy for hot-dip galvanizing for anti-corrosion coating treatment of aluminum materials; the working temperature of the hot-dip galvanizing is 300-400 d
Embodiment 2
[0021] Zinc alloys containing Zr and Ba for hot-dip galvanizing of aluminum alloys at low temperatures. In terms of weight percentage, the chemical composition of the material is: Ba: 0.8wt.%, Zr: 0.5wt.%, In: 0.4wt.%, Mn: 1.8wt.%, V: 0.4wt.%, Bi: 1.5 wt.%, the balance is zinc. Preparation method: Add the above-mentioned raw materials into the atmosphere-protected induction furnace, and use a silicon carbide crucible; induction heat to 550 degrees to form an alloy solution, and use the electromagnetic stirring effect to fully stir for about 10 minutes; put the alloy liquid at 550 degrees After heat preservation and standing for 10 minutes, it is cast into the equipment at the same level as the hot top for semi-continuous casting into required round ingots, and the ingot moving speed is 14m / min. The ingot can be used as a zinc alloy for hot-dip galvanizing for anti-corrosion coating treatment of aluminum materials; the working temperature of the hot-dip galvanizing is 300-400 d
Embodiment 3
[0024]Zinc alloys containing Zr and Ba for hot-dip galvanizing of aluminum alloys at low temperatures. In terms of weight percentage, the chemical composition of the material is: Ba: 0.9wt.%, Zr: 0.6wt.%, In: 0.5wt.%, Mn: 1.8wt.%, V: 0.4wt.%, Bi: 1.5 wt.%, the balance is zinc. Preparation method: Add the above-mentioned raw materials into the atmosphere-protected induction furnace, and use a silicon carbide crucible; induction heat to 550 degrees to form an alloy solution, and use the electromagnetic stirring effect to fully stir for about 10 minutes; put the alloy liquid at 550 degrees After heat preservation and standing for 10 minutes, it is cast into the equipment at the same level as the hot top for semi-continuous casting into required round ingots, and the ingot moving speed is 14m / min. The ingot can be used as a zinc alloy for hot-dip galvanizing for anti-corrosion coating treatment of aluminum materials; the working temperature of the hot-dip galvanizing is 300-400 de
PUM
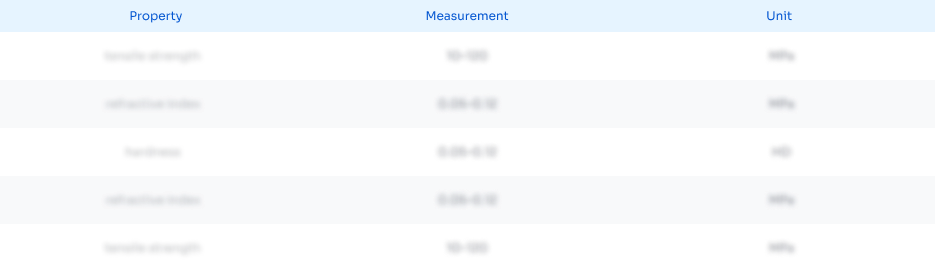
Abstract
Description
Claims
Application Information
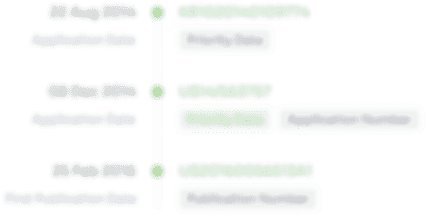
- R&D Engineer
- R&D Manager
- IP Professional
- Industry Leading Data Capabilities
- Powerful AI technology
- Patent DNA Extraction
Browse by: Latest US Patents, China's latest patents, Technical Efficacy Thesaurus, Application Domain, Technology Topic.
© 2024 PatSnap. All rights reserved.Legal|Privacy policy|Modern Slavery Act Transparency Statement|Sitemap