Dual-beam laser welding process defect control method based on acoustical-optical signal monitoring
An acousto-optic signal and laser welding technology, applied in the direction of optical testing flaws/defects, measuring devices, optical devices, etc., can solve the difficulty of double-beam laser welding non-fusion defect detection, can not determine the location of local non-fusion defects, detection means To reduce the risk of unfused defects, optimize the welding process parameters, and simplify the detection process
- Summary
- Abstract
- Description
- Claims
- Application Information
AI Technical Summary
Problems solved by technology
Method used
Examples
Example Embodiment
[0036] Example 1
[0037] Taking the non-fusion defect control of TC4 titanium alloy double-beam laser welding T-joint test plate as an example, the acousto-optic characteristic signal recognition of non-fusion defect of TC4 titanium alloy double-beam laser welding T-joint test plate, welding defects, characteristic signals and process parameters match Relationship establishment, characteristic signal determination of non-fusion defects, identification of defect location and other information, and repair of non-fusion defects through repair welding and other means.
[0038] Its specific implementation process is:
[0039] The first step is to identify the acousto-optic characteristic signals of unfused defects. Install the audible sound, infrared and blue-violet light collection devices on the laser head, on the same plane as the laser incident surface, 150mm away from the welding seam, mark the position information on the welding test plate, collect and record the TC4 titanium
PUM
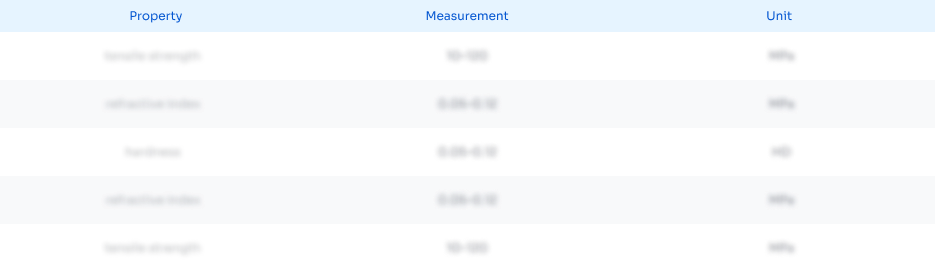
Abstract
Description
Claims
Application Information
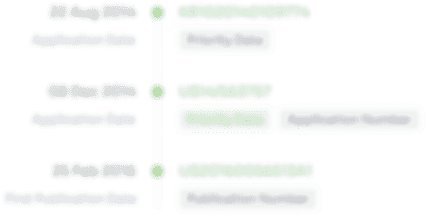
- R&D Engineer
- R&D Manager
- IP Professional
- Industry Leading Data Capabilities
- Powerful AI technology
- Patent DNA Extraction
Browse by: Latest US Patents, China's latest patents, Technical Efficacy Thesaurus, Application Domain, Technology Topic.
© 2024 PatSnap. All rights reserved.Legal|Privacy policy|Modern Slavery Act Transparency Statement|Sitemap