Novel PCB base material cutting knife and manufacturing method thereof
A production method and cutting knife technology, which are applied in metal processing and other directions, can solve the problems of poor replacement of cutting knives, increase production costs, and large loss of substrates, so as to reduce the loss of substrates, reduce the amount of loss, and reduce wear and tear. volume reduction effect
- Summary
- Abstract
- Description
- Claims
- Application Information
AI Technical Summary
Problems solved by technology
Method used
Examples
Example Embodiment
[0025] Example 1
[0026] Such as figure 1 with figure 2 As shown, a new type of PCB substrate cutting knife shown in this embodiment includes a circular base and a plurality of serrations 1 spaced apart on the periphery of the base. The center of the base is provided with a mounting hole 2 with a diameter of 25.4 mm. The base body includes a mounting portion 3 of the inner ring and a connecting portion 4 of the outer ring. The thickness of the mounting portion 3 is greater than the thickness of the connecting portion 4, forming a stepped shape with an inner thickness and a thin outer ring. The thickness of the serration 1 is the same as the thickness of the connecting portion 4; Without changing the structure and operation mode of the existing cutting equipment, the structure of the cutting knife is changed to reduce the thickness of the connection part and the serration of the outer ring of the substrate, which can reduce the amount of loss consumed during the cutting of the subst
Example Embodiment
[0030] Example 2
[0031] Such as figure 2 with image 3 As shown, a new type of PCB substrate cutting knife shown in this embodiment includes a circular base and a plurality of serrations 1 spaced apart on the peripheral edge of the base. The center of the base is provided with a mounting hole 2 with an inner diameter of 25.4 mm. The base body includes a mounting portion 3 of the inner ring and a connecting portion 4 of the outer ring. The thickness of the mounting portion 3 is greater than the thickness of the connecting portion 4, forming a stepped shape with an inner thickness and a thin outer ring. The thickness of the serration 1 is the same as the thickness of the connecting portion 4; Without changing the structure and operation mode of the existing cutting equipment, the structure of the cutting knife is changed to reduce the thickness of the connection part and the serration of the outer ring of the substrate, which can reduce the amount of loss consumed during the cuttin
Example Embodiment
[0036] Example 3
[0037] This embodiment provides a method for manufacturing a novel PCB substrate cutting knife, which includes the following steps:
[0038] S1. Choose a suitable size tungsten steel plate, form a semi-finished plate with a thickness of 3.2mm through high temperature forging, and then cut it into a circular base with an outer diameter of 305mm;
[0039] S2. Drill a mounting hole with a diameter of 25.4mm in the center of the circular base;
[0040] S3. Reduce the thickness of the corresponding connecting part on the substrate (that is, the area from 205mm to 305mm in diameter on the substrate) through the grinding process, so that the remaining thickness of the connecting part is 2.4mm, forming a step shape with inner thickness and thin outer thickness;
[0041] S4. After polishing the substrate, a plurality of diamond serrations with a thickness of 2.4 mm are arranged on the outer peripheral edge of the substrate (that is, the outer peripheral edge of the connecting por
PUM
Property | Measurement | Unit |
---|---|---|
Thickness | aaaaa | aaaaa |
Aperture | aaaaa | aaaaa |
Outer diameter | aaaaa | aaaaa |
Abstract
Description
Claims
Application Information
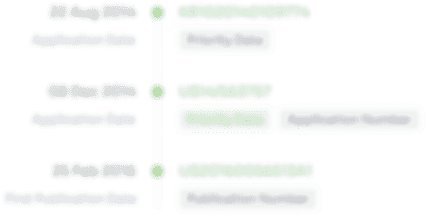
- R&D Engineer
- R&D Manager
- IP Professional
- Industry Leading Data Capabilities
- Powerful AI technology
- Patent DNA Extraction
Browse by: Latest US Patents, China's latest patents, Technical Efficacy Thesaurus, Application Domain, Technology Topic.
© 2024 PatSnap. All rights reserved.Legal|Privacy policy|Modern Slavery Act Transparency Statement|Sitemap