Polyester film
A technology of polyester film and polyester, applied in the field of polyester film, can solve the problems of poor anti-ultraviolet effect and low light transmittance of polyester film, and achieve good product quality, excellent anti-ultraviolet effect, and good light transmittance Effect
- Summary
- Abstract
- Description
- Claims
- Application Information
AI Technical Summary
Benefits of technology
Problems solved by technology
Method used
Examples
Embodiment 1
[0013] A kind of polyester film, is made by the raw material of following weight part:
[0014] 60 parts of polyester optical material, 30 parts of film-grade special masterbatch, 2 parts of polyorganosiloxane, 12 parts of solvent, 2 parts of tricresyl phosphate, 3 parts of curing agent, 1 part of nuciferine and 3 parts of flufentrazone share.
[0015] A method for preparing a polyester film. Firstly, all raw materials are uniformly mixed through a mixer, melted and extruded through an extruder; then the polyester film is prepared by longitudinal stretching and transverse stretching, and finally rolled and packaged.
Embodiment 2
[0017] A kind of polyester film, is made by the raw material of following weight part:
[0018] 80 parts of polyester light material, 20 parts of film-grade special masterbatch, 9 parts of polyorganosiloxane, 4 parts of solvent, 4 parts of tricresyl phosphate, 1 part of curing agent, 2 parts of nuciferine and 2 parts of mefentrazone share.
[0019] A method for preparing a polyester film. Firstly, all raw materials are uniformly mixed through a mixer, melted and extruded through an extruder; then the polyester film is prepared by longitudinal stretching and transverse stretching, and finally rolled and packaged.
Embodiment 3
[0021] A kind of polyester film, is made by the raw material of following weight part:
[0022] 66 parts of polyester light material, 24 parts of special masterbatch for film grade, 8 parts of polyorganosiloxane, 6 parts of solvent, 3 parts of tricresyl phosphate, 2 parts of curing agent, 1.5 parts of nuciferine and 2.8 parts of flufenacet share.
[0023] A method for preparing a polyester film. Firstly, all raw materials are uniformly mixed through a mixer, melted and extruded through an extruder; then the polyester film is prepared by longitudinal stretching and transverse stretching, and finally rolled and packaged.
PUM
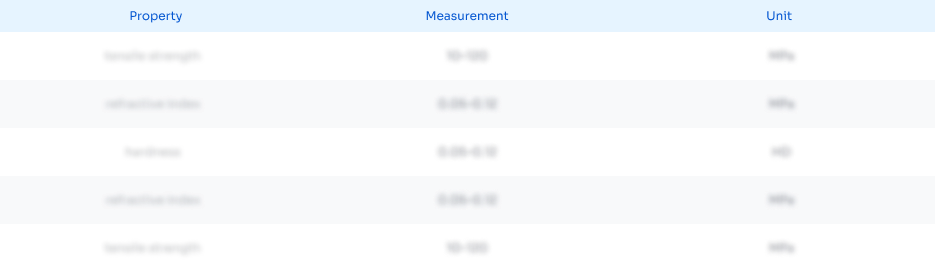
Abstract
Description
Claims
Application Information
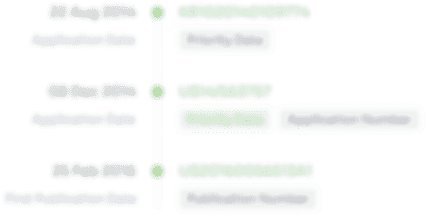
- R&D Engineer
- R&D Manager
- IP Professional
- Industry Leading Data Capabilities
- Powerful AI technology
- Patent DNA Extraction
Browse by: Latest US Patents, China's latest patents, Technical Efficacy Thesaurus, Application Domain, Technology Topic.
© 2024 PatSnap. All rights reserved.Legal|Privacy policy|Modern Slavery Act Transparency Statement|Sitemap