Pressure-sensitive capacitive touch screen
A technology of capacitive screen and touch screen, applied in the field of touch screen, can solve the problems of affecting pressure sensitivity, insufficient covering power, ink drop, etc., and achieve the effect of improving sensitivity, good coating effect, and avoiding voids
- Summary
- Abstract
- Description
- Claims
- Application Information
AI Technical Summary
Benefits of technology
Problems solved by technology
Method used
Image
Examples
Embodiment 1
[0035] like figure 1 As shown, a pressure-sensitive capacitive screen includes a touch screen body, the touch screen body includes a cover glass layer 1 and a first optical adhesive layer 2 arranged under the cover glass layer 1, and the first optical adhesive layer 2 is set Visible area and non-visible area are arranged, and the lower surface of described non-visible area is provided with water-based ink layer 3, and the lower surface of described visible area is provided with transparent flat layer 4, and described water-based ink layer 3 and transparent flat layer The layers 4 are flush; the lower surface of the transparent flat layer 4 is sequentially laminated with a second optical adhesive layer 5, a first electrode layer 6, a third optical adhesive layer 7, a second electrode layer 8, a second optical adhesive layer, and Four optical glue layers 9 and a display screen 10 .
[0036]In the present invention, the first optical adhesive layer 2 is compounded on the lower surf
Embodiment 2
[0048] The difference between this embodiment and embodiment 1 is:
[0049] The third optical adhesive layer 7 is cured by UV optical adhesive, and the UV optical adhesive includes the following raw materials in parts by weight:
[0050]
[0051] Described acrylic acid prepolymer is made by the raw material of following percentage by weight:
[0052]
[0053] The balance is acetone.
[0054] Further, the preparation method of the acrylic acid prepolymer is as follows: methyl methacrylate, propoxylated neopentyl glycol diacrylate, ethoxyethoxy ethyl acrylate, 4-hydroxybutyl Acrylic acid ester, isooctyl methacrylate and azo initiator were added into acetone, mixed uniformly, heated to 60°C, reacted for 4 hours, and then distilled under reduced pressure to obtain the acrylic acid prepolymer.
[0055] Preferably, the kinematic viscosity of the methyl methacrylate is 0.66mm 2 / s, the dynamic viscosity of the 4-hydroxybutyl acrylate is 5.5mPa.s, the dynamic viscosity of the
Embodiment 3
[0061] The difference between this embodiment and embodiment 1 is:
[0062] The third optical adhesive layer 7 is cured by UV optical adhesive, and the UV optical adhesive includes the following raw materials in parts by weight:
[0063]
[0064] Described acrylic acid prepolymer is made by the raw material of following percentage by weight:
[0065]
[0066] The balance is acetone.
[0067] Further, the preparation method of the acrylic acid prepolymer is as follows: methyl methacrylate, propoxylated neopentyl glycol diacrylate, ethoxyethoxy ethyl acrylate, 4-hydroxybutyl Acrylic acid ester, isooctyl methacrylate and azo initiator were added into acetone, mixed uniformly, heated to 55°C, reacted for 2 hours, and then distilled under reduced pressure to obtain the acrylic acid prepolymer.
[0068] Preferably, the kinematic viscosity of the methyl methacrylate is 0.64mm 2 / s, the dynamic viscosity of the 4-hydroxybutyl acrylate is 5.3mPa.s, the dynamic viscosity of the
PUM
Property | Measurement | Unit |
---|---|---|
Thickness | aaaaa | aaaaa |
Thickness | aaaaa | aaaaa |
Thickness | aaaaa | aaaaa |
Abstract
Description
Claims
Application Information
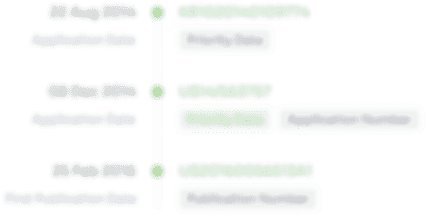
- R&D Engineer
- R&D Manager
- IP Professional
- Industry Leading Data Capabilities
- Powerful AI technology
- Patent DNA Extraction
Browse by: Latest US Patents, China's latest patents, Technical Efficacy Thesaurus, Application Domain, Technology Topic.
© 2024 PatSnap. All rights reserved.Legal|Privacy policy|Modern Slavery Act Transparency Statement|Sitemap