High-surface magnetic flux density dry-pressed permanent ferrite magnet and preparation method thereof
A technology of permanent ferrite and dry pressing, which is applied in the manufacture of inductors/transformers/magnets, the magnetism of inorganic materials, and electrical components, etc. It can solve the problems of reducing production efficiency, reducing friction, and increasing the difficulty of crushing, so as to reduce production Cost and energy consumption, increase the surface magnetic flux density, and the effect of improving the magnetic performance of the product
- Summary
- Abstract
- Description
- Claims
- Application Information
AI Technical Summary
Problems solved by technology
Method used
Image
Examples
Embodiment 1
[0044] (1) Add 200 kg of water to 65 kg of strontium ferrite calcined material, carry out wet ball milling until the average particle size of the powder in the slurry is 0.80 μm, then add 0.5 kg of methyl cellulose, at 29000 r / min Stir for 1 min to obtain a mixed slurry;
[0045] (2) The mixed slurry obtained in step (1) was subjected to wet press molding in a 7000 Oe magnetic field at 25 MPa until the density of the green body was 3.0 g / cm 3 Cylindrical (diameter 30 mm, thickness 15 mm), dried at 120°C for 5 h, crushed to obtain oriented pre-magnetized blocks;
[0046] (3) Add 1.3 kg camphor (100 mesh) to the oriented magnetized block obtained in step (2), mix and pulverize, and pass through a 60-mesh sieve to obtain anisotropic powder;
[0047] (4) Dry press the anisotropic powder obtained in step (3) in a 5000 Oe magnetic field at 20°C and 12 MPa until the density of the green body is 3.1 g / cm 3 Cylindrical (diameter 30 mm, thickness 15 mm), then placed in an electric
Embodiment 2
[0050] (1) Mix 65kg of strontium ferrite pre-fired material with 3.25 kg of CaCO 3 , 1.95 kg Al 2 o 3 and 1.95 kg H 3 BO 3 After mixing, add 35 kg of water, perform wet ball milling until the average particle size of the powder in the slurry is 0.85 μm, then add 0.16 kg of sodium carboxymethyl cellulose, and stir for 10 minutes at 90 r / min to obtain a mixed slurry;
[0051] (2) The mixed slurry obtained in step (1) is subjected to wet press molding in a 4000Oe magnetic field at 16MPa until the density of the green body is 2.8g / cm 3 Cylindrical (diameter 40mm, thickness 20mm), dried at 100°C for 10h, crushed to obtain oriented pre-magnetized blocks;
[0052] (3) Add 0.2 kg of calcium stearate (325 mesh) and 0.4 kg of polyethylene glycol (325 mesh) to the oriented magnetized block obtained in step (2), mix and pulverize, pass through a 40-mesh sieve, and obtain each Anisotropic powder;
[0053] (4) Dry press the anisotropic powder obtained in step (3) in a magnetic field
Embodiment 3
[0056] (1) Mix 65 kg of strontium ferrite pre-fired material with 3.00kg of CaCO 3 and 1.85kg SiO 2 After mixing, add 65 kg of water and carry out wet ball milling until the average particle size of the powder in the slurry is 0.75 μm, then add 0.13 kg of ethyl cellulose and 0.13 kg of hydroxyalkyl cellulose, and stir at 1000 r / min 480 min to obtain mixed slurry;
[0057] (2) The mixed slurry obtained in step (1) was subjected to wet press molding at 12 MPa in a magnetic field of 10000 Oe until the density of the green body was 2.8 g / cm 3 Cylindrical (diameter 40 mm, thickness 10 mm), dried at 80°C for 12 h, crushed to obtain oriented pre-magnetized blocks;
[0058] (3) Add 0.16 kg of stearic acid amide (200 mesh) and 0.16 kg of oleic acid amide (200 mesh) to the oriented magnetized block obtained in step (2), mix and pulverize, pass through a 80-mesh sieve to obtain an isotropic heterosexual powder;
[0059] (4) Dry press the anisotropic powder obtained in step (3) in a
PUM
Property | Measurement | Unit |
---|---|---|
Surface flux density | aaaaa | aaaaa |
Surface flux density | aaaaa | aaaaa |
Surface flux density | aaaaa | aaaaa |
Abstract
Description
Claims
Application Information
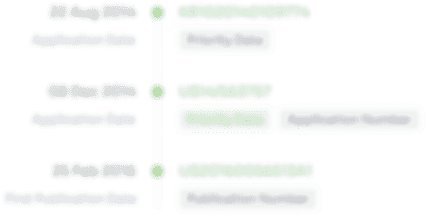
- R&D Engineer
- R&D Manager
- IP Professional
- Industry Leading Data Capabilities
- Powerful AI technology
- Patent DNA Extraction
Browse by: Latest US Patents, China's latest patents, Technical Efficacy Thesaurus, Application Domain, Technology Topic.
© 2024 PatSnap. All rights reserved.Legal|Privacy policy|Modern Slavery Act Transparency Statement|Sitemap