Manufacturing equipment for upper-and-lower intercalated particle layer tool
A manufacturing method and granular layer technology, applied in chemical instruments and methods, dissolving, mixing machines, etc., can solve the problems of low work efficiency and achieve high work efficiency, easy operation and maintenance
- Summary
- Abstract
- Description
- Claims
- Application Information
AI Technical Summary
Problems solved by technology
Method used
Examples
Example Embodiment
[0052] Example 1:
[0053] See Figure 1 to Figure 6 , A method for manufacturing tools with upper and lower layers sandwiched with particles, which includes a bottom liner addition process, an intermediate particle addition process, and a top liner addition process in sequence. The bottom liner addition process refers to laying the bottom liner, so The intermediate particle addition process refers to laying particles on the top surface of the bottom liner to form a particle layer, and the top liner addition process refers to laying a top liner on the top surface of the particle layer; the manufacturing method is based on the top liner. After the board adding process, it also includes the heating coagulation process and the pressure forming process in sequence;
[0054] The bottom liner adding process means that the bottom liner adding device 6 lays a bottom liner into its corresponding groove; the intermediate particle adding process refers to the bottom layer of the particle adding
Example Embodiment
[0057] Example 2:
[0058] The basic content is the same as Example 1, the difference is:
[0059] At least one auxiliary production area 80 is also provided on the surface of the rotating flat disk 2. The number and arrangement sequence of grooves provided in the auxiliary production area 80 are consistent with those of the main production area 8, and the auxiliary production area 80, the main production area The zones 8 are arranged in sequence along the disc surface; after the manufacturing method starts, the auxiliary production zone 80 rotates with the main production zone 8. The five grooves in the auxiliary production zone 80 and the five grooves in the main production zone 8 undergo the same operation. Continuously make moldings, and cycle in turn.
[0060] In addition, the same number of bottom liner adding device 6, particle adding device 3, top liner adding device 7, heating coagulation device 4, pressure forming device 5, and additional bottom liner can be added according t
Example Embodiment
[0061] Example 3:
[0062] The basic content is the same as Example 1, the difference is:
[0063] The particle addition device 3 includes an external addition unit 31, a lifting unit 32, and a horizontal drive unit 33. The discharge port of the external addition unit 31 communicates with the inner cavity of the second groove 82, and the lifting unit 32 includes a lifting motor 321, the lifting rod 322 and the stirring member 323, the lifting motor 321 is set higher than the fixed flat plate 1, the output end of the lifting motor 321 is connected with the top end of the lifting rod 322, the bottom end of the lifting rod 322 passes through the fixed flat plate 1 The stirring member 323 is connected, and the stirring member 323 is located directly above the second groove 82. The part of the lifting rod 322 between the lifting motor 321 and the fixed flat plate 1 is covered with a horizontal drive platform 324, which is connected to the horizontal drive platform 324. The lateral drive u
PUM
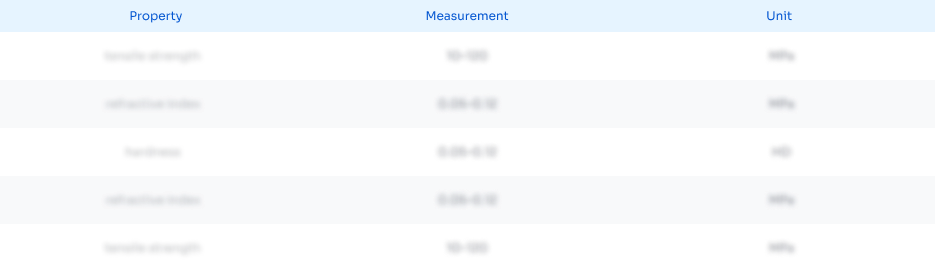
Abstract
Description
Claims
Application Information
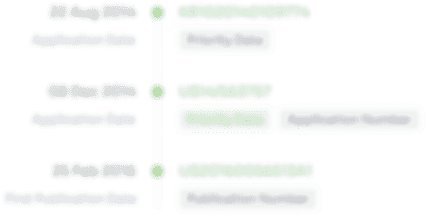
- R&D Engineer
- R&D Manager
- IP Professional
- Industry Leading Data Capabilities
- Powerful AI technology
- Patent DNA Extraction
Browse by: Latest US Patents, China's latest patents, Technical Efficacy Thesaurus, Application Domain, Technology Topic.
© 2024 PatSnap. All rights reserved.Legal|Privacy policy|Modern Slavery Act Transparency Statement|Sitemap