Preparation method of boron-doped porous carbon nitride material
A carbon nitride and boron doping technology, applied in chemical instruments and methods, catalyst activation/preparation, inorganic chemistry, etc., can solve the problems of high reagent cost, unsuitable for commercial promotion and application, complex process, etc., and achieve large adsorption and activation effect, good photocatalytic performance, and simple preparation steps
- Summary
- Abstract
- Description
- Claims
- Application Information
AI Technical Summary
Problems solved by technology
Method used
Examples
Example Embodiment
[0012] Example 1
[0013] Step S1: Fully grind the melamine and put it into a porcelain crucible, seal it and put it in a muffle furnace, heat it up to 550°C at a heating rate of 5°C / min and keep it for 2 hours, cool to room temperature and rinse with boiling water repeatedly to get pure Graphite phase carbon nitride;
[0014] Step S2: Take the graphite phase carbon nitride obtained in step S1, sodium chloride, potassium chloride, and ammonia borane at a mass ratio of 2:1:1:1 and mix them evenly, then spread them in a porcelain boat. The boat was placed in a tube furnace under an air atmosphere, reacted at 750°C for 1 minute, then taken out, cleaned with hot water, and dried in a vacuum drying box to obtain a boron-doped porous carbon nitride material.
Example Embodiment
[0015] Example 2
[0016] Step S1: Fully grind the melamine and put it into a porcelain crucible, seal it and put it in a muffle furnace, heat it up to 550°C at a heating rate of 5°C / min and keep it for 2 hours, cool to room temperature and rinse with boiling water repeatedly to get pure Graphite phase carbon nitride;
[0017] Step S2: Take the graphite phase carbon nitride obtained in step S1, sodium chloride, potassium chloride and ammonia borane at a mass ratio of 2:1:1:1.5, mix them evenly, and then spread them in a porcelain boat. The boat was placed in a tube furnace under an air atmosphere, reacted at 750°C for 2.5 minutes, then taken out, cleaned with hot water, and dried in a vacuum drying box to obtain a boron-doped porous carbon nitride material.
Example Embodiment
[0018] Example 3
[0019] Step S1: Fully grind the melamine and put it into a porcelain crucible, seal it and put it in a muffle furnace, heat it up to 550°C at a heating rate of 5°C / min and keep it for 2 hours, cool to room temperature and rinse with boiling water repeatedly to get pure Graphite phase carbon nitride;
[0020] Step S2: Take the graphite phase carbon nitride obtained in step S1, sodium chloride, potassium chloride and ammonia borane at a mass ratio of 2:1:1:2 and mix them evenly, then spread them in a porcelain boat, and then the porcelain The boat was placed in a tube furnace under an air atmosphere, reacted at 750°C for 2.5 minutes and then taken out, cleaned with hot water, and dried in a vacuum drying box to obtain a boron-doped porous carbon nitride material.
PUM
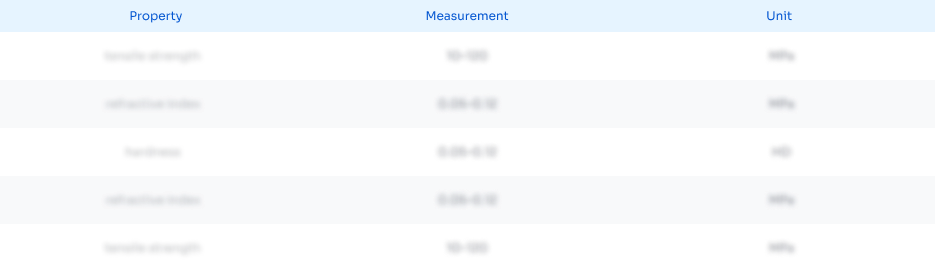
Abstract
Description
Claims
Application Information
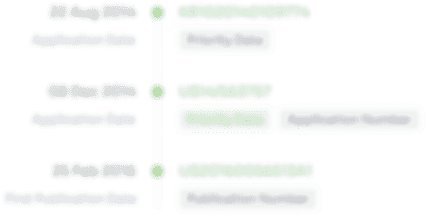
- R&D Engineer
- R&D Manager
- IP Professional
- Industry Leading Data Capabilities
- Powerful AI technology
- Patent DNA Extraction
Browse by: Latest US Patents, China's latest patents, Technical Efficacy Thesaurus, Application Domain, Technology Topic.
© 2024 PatSnap. All rights reserved.Legal|Privacy policy|Modern Slavery Act Transparency Statement|Sitemap