Method for controlling large-size FeGa magnetostrictive single crystal to grow on solid-liquid interface
A magnetostrictive, solid-liquid interface technology, applied in the direction of single crystal growth, crystal growth, single crystal growth, etc., can solve the problems of weakened one-way heat conduction, insufficient heat exchange, etc., and achieve good comprehensive usability and simple process equipment , less volatile effect
- Summary
- Abstract
- Description
- Claims
- Application Information
AI Technical Summary
Problems solved by technology
Method used
Examples
Example Embodiment
[0045] Example 1 Preparation of 30mmFe 81 Ga 19 Single crystal
[0046] The steps used in this embodiment are as follows:
[0047] 1) Ingredients
[0048] The purity of the selected raw materials Fe and Ga are both 99.99wt%, and in order to prevent the Ga element from burning during the smelting process, the Fe 81 Ga 19 Add 2wt% Ga on the basis of the composition. Specifically, 1547.1 g of Fe and 461.8 g of Ga were weighed for use. Before mixing, Fe must be ultrasonically cleaned with absolute ethanol and dried under vacuum to remove oil on the surface.
[0049] 2) Preparation of master alloy ingot
[0050] Put the above-mentioned weighed raw materials Fe and Ga into the crucible of the vacuum non-consumable arc smelting furnace. When placing, it is necessary to place the easily burned Ga element on the bottom of the crucible, and the non-burnable Fe element on the crucible.
[0051] Vacuum the vacuum non-consumable arc melting furnace to 5.0×10 -3 After Pa, fill the furnace body with hig
Example Embodiment
[0063] Example 2 Preparation of 40mmFe 81 Ga 19 Single crystal
[0064] The steps used in this embodiment are as follows:
[0065] 1) Ingredients
[0066] The purity of the selected raw materials Fe and Ga are both greater than 99.99wt%, and in order to prevent the Ga element from burning during the smelting process, the Fe 81 Ga 19 Add 2wt% Ga on the basis of the composition. Specifically, 1547.1 g of Fe and 461.8 g of Ga were weighed for use. Before mixing, Fe must be ultrasonically cleaned with absolute ethanol and dried under vacuum to remove oil on the surface.
[0067] 2) Preparation of master alloy ingot
[0068] Put the above-mentioned weighed raw materials Fe and Ga into the crucible of the vacuum non-consumable arc smelting furnace. When placing, it is necessary to place the easily burned Ga element on the bottom of the crucible, and the non-burnable Fe element on the crucible.
[0069] Vacuum the vacuum non-consumable arc melting furnace to 5.0×10 -3 After Pa, fill the furnace
Example Embodiment
[0080] Example 3 Preparation of 50mmFe 81 Ga 19 Single crystal
[0081] The steps used in this embodiment are as follows:
[0082] 1) Ingredients
[0083] The purity of the selected raw materials Fe and Ga are both greater than 99.99wt%, and in order to prevent Ga element from burning during the smelting process, the Fe 81 Ga 19 Add 2wt% Ga on the basis of the composition. Specifically, 1547.1 g of Fe and 461.8 g of Ga were weighed for use. Fe must be ultrasonically cleaned with absolute ethanol before mixing, and dried under vacuum to remove oil on the surface.
[0084] 2) Preparation of master alloy ingot
[0085] Put the above-mentioned weighed raw materials Fe and Ga into the crucible of the vacuum non-consumable arc smelting furnace. When placing, it is necessary to place the easily burned Ga element on the bottom of the crucible, and the non-burnable Fe element on the crucible.
[0086] Vacuum non-consumable arc melting furnace to 5.0×10 -3 After Pa, fill the furnace body with high-
PUM
Property | Measurement | Unit |
---|---|---|
The inside diameter of | aaaaa | aaaaa |
Length | aaaaa | aaaaa |
Saturation magnetostriction coefficient | aaaaa | aaaaa |
Abstract
Description
Claims
Application Information
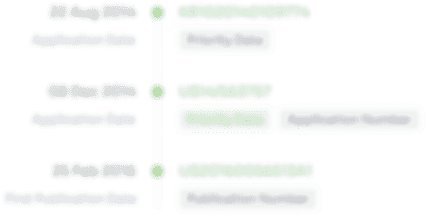
- R&D Engineer
- R&D Manager
- IP Professional
- Industry Leading Data Capabilities
- Powerful AI technology
- Patent DNA Extraction
Browse by: Latest US Patents, China's latest patents, Technical Efficacy Thesaurus, Application Domain, Technology Topic.
© 2024 PatSnap. All rights reserved.Legal|Privacy policy|Modern Slavery Act Transparency Statement|Sitemap