Catalyst for removing nitric oxide and preparation method thereof
- Summary
- Abstract
- Description
- Claims
- Application Information
AI Technical Summary
Benefits of technology
Problems solved by technology
Method used
Image
Examples
Embodiment 1
[0040] 50 g of silica sol (40% SiO 2) mixed with aluminum nitrate aqueous solution containing 75 grams of aluminum oxide, fully stirred, placed in a three-necked bottle, and added dropwise with silver nitrate solution containing 5 grams of silver oxide, while vigorously electromagnetically stirring, maintaining the temperature of the oil bath at 70 ° C, loading The sol was solidified after stirring for three hours, and the stirring was stopped, and the temperature was raised to 100°C, and the solvent was evaporated for 12 hours. Transfer to a crucible, bake with an infrared lamp for 24 hours, then transfer to a muffle furnace at 700 ° C for 6 hours, and crush to 40-60 meshes to obtain the desired Ag-containing powder. 2 O 5% Ag / SiO 2 -Al 2 o 3 catalyst.
Embodiment 2
[0042] 50 g of silica sol (40% SiO 2 ) mixed with aluminum nitrate aqueous solution containing 75 grams of aluminum oxide, fully stirred, placed in a three-necked bottle, and added dropwise with silver nitrate solution containing 3 grams of silver oxide, while vigorously electromagnetically stirring, maintaining the temperature of the oil bath at 70 ° C, loading The sol was solidified after stirring for three hours, and the stirring was stopped, and the temperature was raised to 100°C, and the solvent was evaporated for 12 hours. Transfer to a crucible, bake with an infrared lamp for 24 hours, then transfer to a muffle furnace for 6 hours at 700°C, grind to 40-60 meshes, impregnate in an equal volume of titanium nitrate solution containing 2 grams of titanium oxide for 12 hours, and dry at 120°C Calcined in a muffle furnace at 450°C to obtain the desired 2% TiO 2 Modified, containing Ag 2 O 3% Ag / SiO 2 -Al 2 o 3 catalyst.
Embodiment 3
[0044] 125 g of silica sol (40% SiO 2 ) mixed with an aqueous solution of aluminum sulfate containing 47.8 grams of aluminum oxide, fully stirred, placed in a three-necked bottle, and added dropwise with a silver nitrate solution containing 0.2 grams of silver oxide, while vigorously stirring electromagnetically to maintain the temperature of the oil bath at 70 ° C. Return to the condensing tube, stir for three hours and then the sol solidifies, stop stirring, raise the temperature to 150°C, and evaporate the solvent for 12 hours. Transfer to a crucible, bake with an infrared lamp for 24 hours, then transfer to a muffle furnace and bake at 500°C for 8 hours, crush to 40-60 meshes, then impregnate with equal volume of zirconium nitrate solution containing 2 grams of zirconia for 12 hours, and dry at 80°C Roasted in a muffle furnace at 600°C to obtain the required 2% ZrO 2 Modified, containing Ag 2 O 0.2% Ag / SiO 2 -Al 2 o 3 catalyst.
PUM
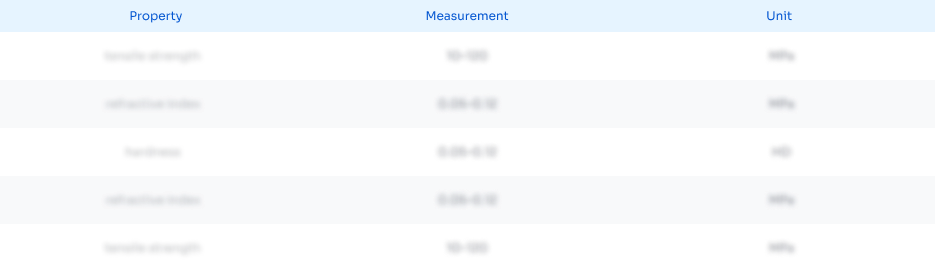
Abstract
Description
Claims
Application Information
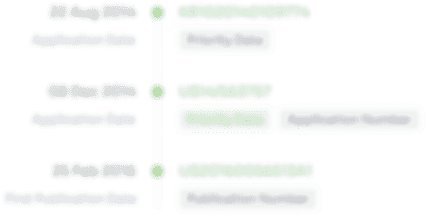
- R&D Engineer
- R&D Manager
- IP Professional
- Industry Leading Data Capabilities
- Powerful AI technology
- Patent DNA Extraction
Browse by: Latest US Patents, China's latest patents, Technical Efficacy Thesaurus, Application Domain, Technology Topic.
© 2024 PatSnap. All rights reserved.Legal|Privacy policy|Modern Slavery Act Transparency Statement|Sitemap