Method for adjusting amount of spinning stagger of two spinning wheels
A spinning wheel and offset technology, which is applied in the field of adjusting the offset amount of two-wheel spinning, can solve the problems of cumbersome calculation process, poor stability, and poor scientific applicability, and achieve simple operation, high stability, and good applicability sexual effect
- Summary
- Abstract
- Description
- Claims
- Application Information
AI Technical Summary
Problems solved by technology
Method used
Image
Examples
Embodiment 1
[0050] This embodiment is a method for adjusting the amount of spinning offset in the processing of ultra-high-strength steel thin-walled cylindrical parts by the two-wheel offset spinning method.
[0051] The structure of the rotary wheels used in the processing process is exactly the same, the number of rotary wheels N is 2, the diameter of the rotary wheels D is 300mm, the thickness of the rotary wheels d is 70mm, the angle of rotation of the rotary wheels is 30°, and the thickness of the rotary wheel screw-in ends is d 0 is 35mm, the exit angle β of the rotary wheel is 30°, and the fillet radius R of the rotary wheel is 6mm.
[0052] The concrete process of this embodiment is:
[0053] Step 1, determine the basic parameters of the wheel.
[0054] The number N of said rotary wheels is 2, and each rotary wheel has the same structure. The basic parameters of the rotary wheel include the rotary wheel diameter D, the rotary wheel thickness d, the rotary wheel screw-in angle α, the
Embodiment 2
[0078] This embodiment is a method for adjusting the amount of spinning offset in the processing of ultra-high-strength steel thin-walled cylindrical parts by the two-wheel offset spinning method.
[0079] The structure of the rotary wheels used in the processing process is exactly the same, the number of rotary wheels N is 2, the diameter of the rotary wheels D is 300mm, the thickness of the rotary wheels d is 70mm, the angle of rotation of the rotary wheels is 30°, and the thickness of the rotary wheel screw-in ends is d 0 is 35mm, the exit angle β of the rotary wheel is 30°, and the fillet radius R of the rotary wheel is 6mm.
[0080] The concrete process of this embodiment is:
[0081] Step 1, determine the basic parameters of the wheel.
[0082] The number N of said rotary wheels is 2, and each rotary wheel has the same structure. The basic parameters of the rotary wheel include the rotary wheel diameter D, the rotary wheel thickness d, the rotary wheel screw-in angle α, t
Embodiment 3
[0106] This embodiment is a method for adjusting the amount of spinning offset in the processing of ultra-high-strength steel thin-walled cylindrical parts by the two-wheel offset spinning method.
[0107] The structure of the roller used in the processing process is exactly the same, the number N of the roller is 2, the diameter D of the roller is 300mm, the thickness d of the roller is 70mm, the angle of rotation of the roller is α is 30°, and the thickness of the end of the roller is d 0 is 35mm, the exit angle β of the rotary wheel is 30°, and the fillet radius R of the rotary wheel is 6mm.
[0108] The concrete process of this embodiment is:
[0109] Step 1, determine the basic parameters of the wheel.
[0110] The number N of said rotary wheels is 2, and each rotary wheel has the same structure. The basic parameters of the rotary wheel include the rotary wheel diameter D, the rotary wheel thickness d, the rotary wheel screw-in angle α, the rotary wheel screw-in end thickn
PUM
Property | Measurement | Unit |
---|---|---|
Diameter | aaaaa | aaaaa |
Thickness | aaaaa | aaaaa |
Abstract
Description
Claims
Application Information
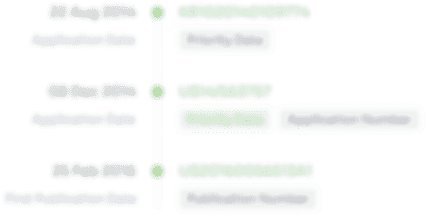
- R&D Engineer
- R&D Manager
- IP Professional
- Industry Leading Data Capabilities
- Powerful AI technology
- Patent DNA Extraction
Browse by: Latest US Patents, China's latest patents, Technical Efficacy Thesaurus, Application Domain, Technology Topic.
© 2024 PatSnap. All rights reserved.Legal|Privacy policy|Modern Slavery Act Transparency Statement|Sitemap