Direct-spun polyester colored staple fiber production equipment and direct-spun polyester colored staple fiber production method
A production method and production equipment technology, applied in the direction of spinning solution preparation, adding pigments in spinning solution, adding dyes in spinning solution, etc., can solve the problem of reducing the mechanical properties of polyester colored yarn, affecting the quality of colored fibers, and the production process Complicated and other issues, to achieve good color fastness and weather resistance, save costs, and improve the effect of service life
- Summary
- Abstract
- Description
- Claims
- Application Information
AI Technical Summary
Benefits of technology
Problems solved by technology
Method used
Image
Examples
Embodiment 1
[0028] A kind of direct spinning polyester colored staple fiber production equipment, such as figure 1 As shown, it includes the melt pipeline and the twin-screw extruder respectively connected by the same metering pump, the twin-screw extruder is connected back to the melt pipeline through the booster pump, and the final melt pipeline is connected to the dynamic mixer and the static mixer in sequence , metering pump and spinning box.
[0029] Specifically, such as figure 2 , 3 As shown, the dynamic mixer includes a barrel 1, a rotating shaft 2 installed on the central axis of the barrel 1 and rotating, the rotating shaft 2 is uniformly provided with pins 3 along its length, and a row is arranged every 90°; each pin 3 One end is fixed on the rotating shaft 2, and the other end protrudes vertically. The inner wall of the barrel 1 and the surface of the rotating shaft 2 are provided with evenly distributed crescent-shaped grooves 4, and the concave surfaces of all the crescent-
Embodiment 2
[0037] Mixing: The flow rate of the polyester melt pipeline is set to 29.5Kg / min, and 30wt% of the polyester melt is introduced into the twin-screw extruder through a metering pump. ℃ / 280℃ / 280℃ / 280℃, twin-screw speed 60r / min, mix a red organic pigment, polyester wax dispersant and antioxidant 1010 in a certain ratio (100:5:2) and add to the meter , adding polyester melt through a meter, and shearing and blending in a twin-screw extruder;
[0038] Dynamic mixing: re-enter the polyester melt pipeline through the booster pump, and enter the dynamic mixer and static mixer to mix evenly into colored polyester melt;
[0039] Spinning: the colored melt enters the spinning box for spinning, the temperature of the spinning box is 288°C, the number of spinning positions is 17, the fineness of the precursor is 5.34dtex, and the spinning speed is 1085m / min; the effective content of pigment in the fiber is 1.5wt% ;
[0040]Post-spinning: raw silk bundle, drafting treatment, the
Embodiment 3
[0042] Mixing: The flow rate of the polyester melt pipeline is set to 29.5Kg / min, and 10wt% of the polyester melt is introduced into the twin-screw extruder through a metering pump. The temperature settings of the five zones of the twin-screw extruder are respectively 275°C / 275 ℃ / 275℃ / 275℃ / 275℃, twin-screw speed 50r / min, mix a blue organic pigment, polyethylene wax dispersant and antioxidant 1010 in a certain ratio (100:1:2) and then add and measure The organic pigment is added into the polyester melt through the meter, and sheared and blended in the twin-screw extruder;
[0043] Dynamic mixing: re-enter the polyester melt pipeline through the booster pump, and enter the dynamic mixer and static mixer to mix evenly into colored polyester melt;
[0044] Spinning: the colored melt enters the spinning box for spinning, the temperature of the spinning box is 288°C, the number of spinning positions is 17, the fineness of the precursor is 5.34dtex, and the spinning speed is
PUM
Property | Measurement | Unit |
---|---|---|
Diameter | aaaaa | aaaaa |
Length | aaaaa | aaaaa |
Height | aaaaa | aaaaa |
Abstract
Description
Claims
Application Information
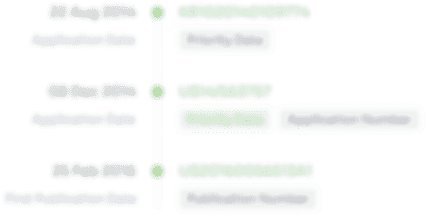
- R&D Engineer
- R&D Manager
- IP Professional
- Industry Leading Data Capabilities
- Powerful AI technology
- Patent DNA Extraction
Browse by: Latest US Patents, China's latest patents, Technical Efficacy Thesaurus, Application Domain, Technology Topic.
© 2024 PatSnap. All rights reserved.Legal|Privacy policy|Modern Slavery Act Transparency Statement|Sitemap