Amorphous alloy ultrasound-assisted induction heating welding equipment and method
An induction heating welding, amorphous alloy technology, applied in auxiliary welding equipment, welding equipment, welding equipment and other directions, can solve problems such as hindering the contact and wetting of the surface to be welded, the quality of materials cannot be guaranteed, and the material properties are adversely affected. , to achieve the effect of improving synthesis efficiency, improving welding quality and excellent mechanical properties
- Summary
- Abstract
- Description
- Claims
- Application Information
AI Technical Summary
Problems solved by technology
Method used
Image
Examples
Embodiment Construction
[0041] The present application is further described in conjunction with the following examples.
[0042] Such as figure 1 , a kind of amorphous alloy ultrasonic-assisted induction heating welding equipment, used to realize the above-mentioned amorphous alloy ultrasonic-assisted induction heating welding method, the amorphous alloy ultrasonic-assisted induction heating welding equipment includes a base 1, a furnace body 2, a processing Platform 3, electric heating system 4, gas delivery system 5 and ultrasonic auxiliary system 6. Wherein, the furnace body 2 is arranged on the base 1; the processing platform 3 is arranged on the furnace body 2 for placing the amorphous alloy to be welded; the electric heating system 4 is located above the processing platform 3; The system 5 is located above the processing platform 3 and is used to transport inert gas, the inert gas being argon or helium; the ultrasonic auxiliary system 6 is arranged on the processing platform 3 and is located on o
PUM
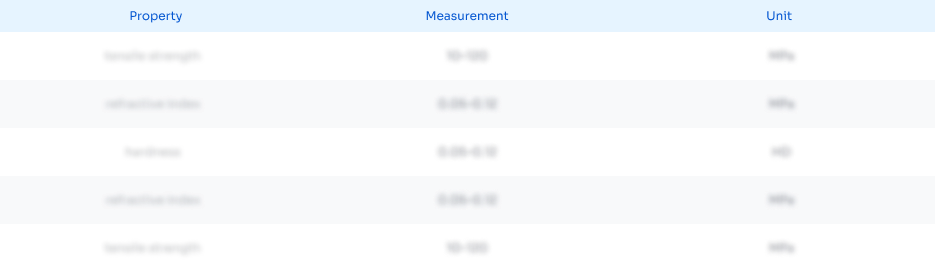
Abstract
Description
Claims
Application Information
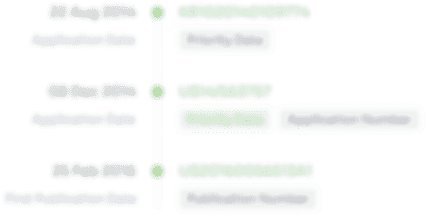
- R&D Engineer
- R&D Manager
- IP Professional
- Industry Leading Data Capabilities
- Powerful AI technology
- Patent DNA Extraction
Browse by: Latest US Patents, China's latest patents, Technical Efficacy Thesaurus, Application Domain, Technology Topic.
© 2024 PatSnap. All rights reserved.Legal|Privacy policy|Modern Slavery Act Transparency Statement|Sitemap