Manufacturing method of aluminum alloy three-layer composite material for brazing
A technology of brazing layer and aluminum alloy, which is applied in the field of aluminum alloy manufacturing, can solve the problems of corrosion and strength, complex production process, and large energy consumption, so as to ensure mechanical properties and corrosion properties, meet brazing requirements, The effect of increasing strength
- Summary
- Abstract
- Description
- Claims
- Application Information
AI Technical Summary
Benefits of technology
Problems solved by technology
Method used
Image
Examples
Embodiment Construction
[0035] Embodiments of the present invention are described below through specific examples, and those skilled in the art can easily understand other advantages and effects of the present invention from the content disclosed in this specification. The present invention can also be implemented or applied through other different specific implementation modes, and various modifications or changes can be made to the details in this specification based on different viewpoints and applications without departing from the spirit of the present invention.
[0036] according to figure 1 The flow chart of the preparation method of the aluminum alloy three-layer composite material for brazing shown in the present invention, a preparation method of the aluminum alloy three-layer composite material for brazing, comprises the following steps:
[0037] A. Ingredients: Calculate the amount of various alloy ingots and intermediate alloys used to prepare the brazing layer and base layer ingots and pr
PUM
Property | Measurement | Unit |
---|---|---|
Thickness | aaaaa | aaaaa |
Abstract
Description
Claims
Application Information
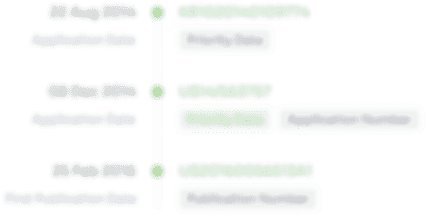
- R&D Engineer
- R&D Manager
- IP Professional
- Industry Leading Data Capabilities
- Powerful AI technology
- Patent DNA Extraction
Browse by: Latest US Patents, China's latest patents, Technical Efficacy Thesaurus, Application Domain, Technology Topic.
© 2024 PatSnap. All rights reserved.Legal|Privacy policy|Modern Slavery Act Transparency Statement|Sitemap