Magnetic suspension type side pressure one-way micro-power piezoelectric inertia driver
A driver and micro-power technology, applied to piezoelectric effect/electrostrictive or magnetostrictive motors, magnetic attraction or thrust holding devices, electrical components, etc., can solve problems such as output performance changes and inability to move
- Summary
- Abstract
- Description
- Claims
- Application Information
AI Technical Summary
Benefits of technology
Problems solved by technology
Method used
Image
Examples
Embodiment Construction
[0028] The following are specific embodiments of the present invention and in conjunction with the accompanying drawings, the technical solutions of the present invention are further described, but the present invention is not limited to these embodiments.
[0029] Such as figure 1 and figure 2 As shown, the magnetic levitation type side pressure unidirectional microdynamic piezoelectric inertia driver includes a bracket body 1 and a driver body 2, the driver body 2 includes a bracket block 3, a pressure plate 4 fixedly arranged on the bracket block 3, and the edges are clamped on the pressure plate 4 The piezoelectric sheet 5 on the top of the piezoelectric sheet 5 is electrically connected with an asymmetric waveform electric signal.
[0030] During operation, the piezoelectric sheet 5 is excited by an asymmetric waveform electric signal, so that the piezoelectric sheet 5 generates inertial impact forces of different magnitudes in the positive and negative directions.
[003
PUM
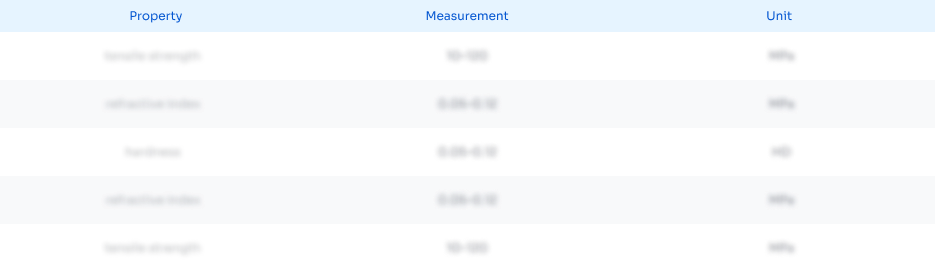
Abstract
Description
Claims
Application Information
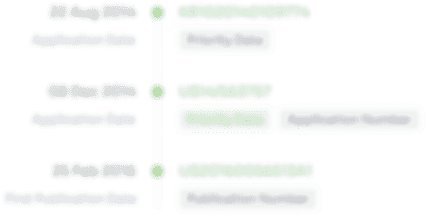
- R&D Engineer
- R&D Manager
- IP Professional
- Industry Leading Data Capabilities
- Powerful AI technology
- Patent DNA Extraction
Browse by: Latest US Patents, China's latest patents, Technical Efficacy Thesaurus, Application Domain, Technology Topic.
© 2024 PatSnap. All rights reserved.Legal|Privacy policy|Modern Slavery Act Transparency Statement|Sitemap