Method Of Producing Film And Method Of Producing Ink-Jet Head
a production method and inkjet head technology, applied in the direction of printing, pressure inorganic powder coating, coating, etc., can solve the problems of film damage, film even destruction, fault or defect generation in film, etc., to prevent the destruction of film, improve the quality of film formation performance and the quality of formed film, and suppress the amount of gas generated
- Summary
- Abstract
- Description
- Claims
- Application Information
AI Technical Summary
Benefits of technology
Problems solved by technology
Method used
Image
Examples
examples
[0067] Next, the present invention will be explained in further detail by examples.
Examples and Comparative Examples for Investigating the Effect on the Film by the Presence or Absence of Heating Treatment to the Material Particles
example 1-1
1. Formation of Film
(1) Preparation of Ceramic Particles
[0068] As the material, α-alumina (obtained from Showa Denko Kabushiki Kaisha) was pulverized with a ball mill to obtain fine powder of α-alumina having a mean particle diameter of about 1 μm and a particle size distribution as shown in FIG. 10. The particle size distribution was measured by using a dry type particle-size distribution measuring apparatus (HELOS & RODOS, manufactured by Japan Laser Corporation). This fine powder was placed in a muffle furnace (FP100, manufactured by Yamato Scientific Co., Ltd.), and the temperature in the furnace was raised up to 600° C. by taking one hour. After holding the temperature at 600° C. for one hour, the inside of the furnace was cooled by natural cooling, and the fine powder was taken out. FIG. 10 also shows a particle size distribution of α-alumina after the heating treatment.
(2) Film Formation
[0069] Stainless steel plate (SUS430) was used as the substrate, and the α-alumina pow
example 1-2
[0072] Particles of α-alumina were prepared and a film was formed in a similar manner as in Example 1-1 except that the thickness of the formed insulating film was 1 μm, and the measurement was performed.
PUM
Property | Measurement | Unit |
---|---|---|
Temperature | aaaaa | aaaaa |
Temperature | aaaaa | aaaaa |
Temperature | aaaaa | aaaaa |
Abstract
Description
Claims
Application Information
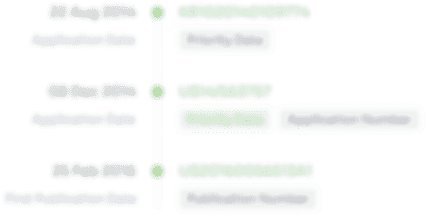
- R&D Engineer
- R&D Manager
- IP Professional
- Industry Leading Data Capabilities
- Powerful AI technology
- Patent DNA Extraction
Browse by: Latest US Patents, China's latest patents, Technical Efficacy Thesaurus, Application Domain, Technology Topic.
© 2024 PatSnap. All rights reserved.Legal|Privacy policy|Modern Slavery Act Transparency Statement|Sitemap