Composite material for vehicles
A technology for composite materials and vehicles, which is applied to vehicle parts, vehicle seats, special positions of vehicles, etc., and can solve problems such as wrinkles that are not considered
- Summary
- Abstract
- Description
- Claims
- Application Information
AI Technical Summary
Problems solved by technology
Method used
Image
Examples
Embodiment 1~10
[0071] will use figure 1 The fabric woven with the double-layer structure shown is used as the skin material, and the polyurethane foam sheet is laminated on the back of the fabric as the lining material by the flame lamination method according to the conditions shown in the following Table 1, and the composite materials for vehicles of Examples 1 to 10 are obtained. Material. The thickness of the laminated polyurethane foam sheet was 1.3 mm. In the composite materials for vehicles of Examples 1 to 10, the woven fabric as the skin material has a wide gap between adjacent yarns and has a floating gap structure formed by the gap.
[0072] For the fabric used as the skin material in the vehicle composite material of Example 1, 167dtex / 48f×2 2H twisted yarn (300 denier) and 167dtex / 48f twisted yarn (150 denier) are alternately used as warp yarn, and 167dtex / 48f twisted yarn (150 denier) is used as weft yarn. 48f×2 2H twisted yarn (300 denier), set the on-machine density of th
Embodiment 11~25
[0081] will use figure 2 The fabric woven with the single-layer structure shown was used as the skin material, and a polyurethane foam sheet was laminated on its back side as a lining material by a flame lamination method according to the conditions shown in the following Table 2, and the vehicles of Examples 11 to 25 were obtained. composite material. The thickness of the laminated polyurethane foam sheet was 1.3 mm. In the composite materials for vehicles of Examples 11 to 25, the woven fabrics used as the skin materials all have a wide gap between adjacent yarns and a floating gap structure formed by the gap.
[0082] For the fabric used as the skin material in the vehicle composite material of Example 11, the twisted yarn (150 denier) of 167dtex / 48f is used as the warp yarn, and the twisted yarn (150 denier) of 167dtex / 48f is used as the weft yarn. The density is set to 75 pieces / 25.4mm, use figure 2 Tissue 1 weaving is shown. The number of floating yarns in the w
PUM
Property | Measurement | Unit |
---|---|---|
Thickness | aaaaa | aaaaa |
Abstract
Description
Claims
Application Information
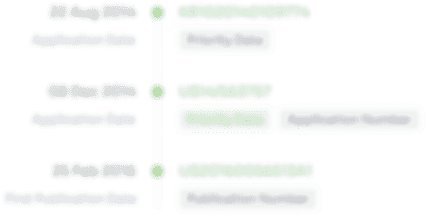
- R&D Engineer
- R&D Manager
- IP Professional
- Industry Leading Data Capabilities
- Powerful AI technology
- Patent DNA Extraction
Browse by: Latest US Patents, China's latest patents, Technical Efficacy Thesaurus, Application Domain, Technology Topic.
© 2024 PatSnap. All rights reserved.Legal|Privacy policy|Modern Slavery Act Transparency Statement|Sitemap