Production process of solar support frame aluminum alloy profile
An aluminum alloy profile and production process technology, which is applied in the field of aluminum profile forming, can solve the problems of high difficulty, large number of unqualified, and high requirements for the production process of solar brackets, so as to save production costs, simplify the process flow, and reduce the number of unqualified products. effect of probability
- Summary
- Abstract
- Description
- Claims
- Application Information
AI Technical Summary
Benefits of technology
Problems solved by technology
Method used
Image
Examples
Embodiment 1
[0027] Such as figure 1 As shown, a production process of aluminum alloy profiles for solar bracket frames, the production steps are as follows:
[0028] S1. Select raw materials; the percentages of each element in the raw materials are: Si, 0.38%~0.42%, Mg, 0.53%~0.57%, Fe not more than 0.18%, and the remaining elements are Al;
[0029] S2. Smelting: melting the raw materials in step S1 at a melting temperature of 720°C to 760°C;
[0030] S3. Casting; casting is carried out by semi-continuous direct water-cooling casting method, the casting temperature is 710°C~730°C, the casting speed is 50~70mm / min, and the cooling water pressure is 0.1~0.3MPa; The speed block refines the casting structure and increases the density of the structure, thereby improving the mechanical properties and heat treatment effect.
[0031] S4, homogenize the cast rod structure;
[0032] S5, extruding the cast rod processed in step S4 to obtain an aluminum profile;
[0033] S6, adopt straightening ma
Embodiment 2
[0054] A kind of production process of aluminum alloy profile of solar support frame, its production steps are as follows:
[0055] S1. Select raw materials; the percentages of each element in the raw materials are: Si, 0.42%, Mg, 0.57%, Fe is not more than 0.18%, and the remaining elements are Al;
[0056] S2. Smelting: melting the raw materials in step S1 at a melting temperature of 720°C to 760°C;
[0057] S3. Casting; casting is carried out by semi-continuous direct water-cooling casting method, the casting temperature is 710°C~730°C, the casting speed is 50~70mm / min, and the cooling water pressure is 0.1~0.3MPa; The speed block refines the casting structure and increases the density of the structure, thereby improving the mechanical properties and heat treatment effect.
[0058] S4, homogenize the cast rod structure;
[0059] S5, extruding the cast rod processed in step S4 to obtain an aluminum profile;
[0060] S6, adopt straightening machine to straighten the aluminum
Embodiment 3
[0081] A kind of production process of aluminum alloy profile of solar support frame, its production steps are as follows:
[0082] S1. Select raw materials; the percentages of each element in the raw materials are: Si, 0.40%, Mg, 0.55%, Fe is not more than 0.18%, and the remaining elements are Al;
[0083] S2, smelting; melting the raw materials in step S1 at a melting temperature of 740°C;
[0084] S3. Casting; casting is carried out by semi-continuous direct water-cooling casting method, the casting temperature is 710°C~730°C, the casting speed is 50~70mm / min, and the cooling water pressure is 0.1~0.3MPa; The speed block refines the casting structure and increases the density of the structure, thereby improving the mechanical properties and heat treatment effect.
[0085] S4, homogenize the cast rod structure;
[0086] S5, extruding the cast rod processed in step S4 to obtain an aluminum profile;
[0087] S6, adopt straightening machine to straighten the aluminum profile
PUM
Property | Measurement | Unit |
---|---|---|
Thickness | aaaaa | aaaaa |
Abstract
Description
Claims
Application Information
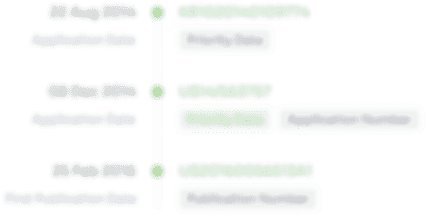
- R&D Engineer
- R&D Manager
- IP Professional
- Industry Leading Data Capabilities
- Powerful AI technology
- Patent DNA Extraction
Browse by: Latest US Patents, China's latest patents, Technical Efficacy Thesaurus, Application Domain, Technology Topic.
© 2024 PatSnap. All rights reserved.Legal|Privacy policy|Modern Slavery Act Transparency Statement|Sitemap