Method for welding magnesium target and copper back plate
A welding method and copper backplane technology, which is applied in the field of target material manufacturing, can solve problems such as insufficient metallurgical bonding between brazing filler metal and backplane, magnesium target oxidation, etc., and achieve the effects of eliminating oxidation, improving welding bonding strength, and enhancing welding strength
- Summary
- Abstract
- Description
- Claims
- Application Information
AI Technical Summary
Benefits of technology
Problems solved by technology
Method used
Image
Examples
example 1
[0030] Example 1: Welding a magnesium target with a diameter of 160mm:
[0031] After the magnesium target and the copper back plate were polished with a steel brush, they were cleaned in acetone to remove oil stains, and then in 50g / L NaOH, 10g / LNa 3 PO 4 After washing with alkaline solution for 15s, wash with deionized water and dry in vacuum.
[0032] Place the magnesium target material, the back plate, and the solder block on the heating platform 1, wherein the solder block is respectively placed on the welding surface of the magnesium target material and the back plate, and the sealing cover 2 is put on the vacuum to 100Pa, and argon gas is introduced. Make the internal air pressure an atmospheric pressure; turn on the heating platform and set the temperature to 180°C, and keep the temperature constant until the solder is completely melted.
[0033] Operate the hand-held ultrasonic instrument through the hand hole, apply the brazing material repeatedly to completely in
example 2
[0039] Example 2: Welding a magnesium target with a diameter of 180mm:
[0040] After the magnesium target and the copper back plate were polished with a steel brush, they were cleaned in acetone to remove oil stains, and then in 50g / L NaOH, 10g / LNa 3 PO 4 After washing with alkaline solution for 20s, wash with deionized water and then vacuum dry.
[0041] Place the magnesium target material, the back plate, and the solder block on the heating platform 1, wherein the solder block is placed on the welding surface of the magnesium target material and the back plate respectively, cover the sealing cover 2 and evacuate to 200Pa, and pass in argon gas, Make the internal air pressure an atmospheric pressure; turn on the heating platform and set the temperature to 190°C, and keep the temperature constant until the solder is completely melted.
[0042] Operate the hand-held ultrasonic instrument through the hand hole, apply the brazing material repeatedly to completely infiltrate t
example 3
[0048] Example 3: Welding a magnesium target with a diameter of 200mm:
[0049] After the magnesium target and the copper back plate were polished with a steel brush, they were cleaned in acetone to remove oil stains, and then in 50g / L NaOH, 10g / LNa 3 PO 4After washing with alkaline solution for 20s, wash with deionized water and then vacuum dry.
[0050] Place the magnesium target material, the back plate, and the solder block on the heating platform 1, wherein the solder block is placed on the welding surface of the magnesium target material and the back plate respectively, cover the sealing cover 2 and evacuate to 300Pa, and pass in argon gas, Make the internal air pressure an atmospheric pressure; turn on the heating platform and set the temperature to 200°C, and keep the temperature constant until the solder is completely melted.
[0051] Operate the hand-held ultrasonic instrument through the hand hole, apply the brazing material repeatedly to completely infiltrate th
PUM
Property | Measurement | Unit |
---|---|---|
Welding strength | aaaaa | aaaaa |
Abstract
Description
Claims
Application Information
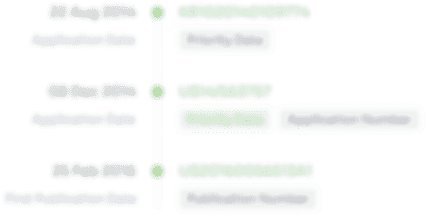
- R&D Engineer
- R&D Manager
- IP Professional
- Industry Leading Data Capabilities
- Powerful AI technology
- Patent DNA Extraction
Browse by: Latest US Patents, China's latest patents, Technical Efficacy Thesaurus, Application Domain, Technology Topic.
© 2024 PatSnap. All rights reserved.Legal|Privacy policy|Modern Slavery Act Transparency Statement|Sitemap