Novel AMT friction plate assembly of riveted structure
A technology of riveting structure and friction plate, applied in the field of clutch, can solve the problems of deformation of metal base, reduction of friction coefficient of friction plate, etc., and achieve the effects of low production cost, stable friction coefficient and good wear resistance.
- Summary
- Abstract
- Description
- Claims
- Application Information
AI Technical Summary
Benefits of technology
Problems solved by technology
Method used
Image
Examples
Embodiment 1
[0023] A riveted structure AMT new friction plate assembly, mainly composed of a ceramic friction plate 1, a metal base A2 and a metal base B3; the ceramic friction plate 1 is sintered on the metal base A2; the metal base A2 and the metal base Coaxial riveting hole I5 and riveting relief hole I6 are respectively provided on B3, the metal base A2 is riveted on the metal base B3 through rivet I9, and the rivet head of rivet I9 falls on the riveting relief hole I6 on the symmetrical side . The metal base A2 and the metal base B3 are also respectively provided with coaxial riveting hole II4 and riveting relief hole II7, and the metal base A2 and the metal base B3 are riveted in the driven disk assembly through the rivet II10, The rivet head of the rivet II10 falls at the riveting relief hole II7 on the symmetrical side.
[0024] In this embodiment, the ceramic friction plate 1 has a relatively high coefficient of friction and can work at a relatively high temperature for a long time
PUM
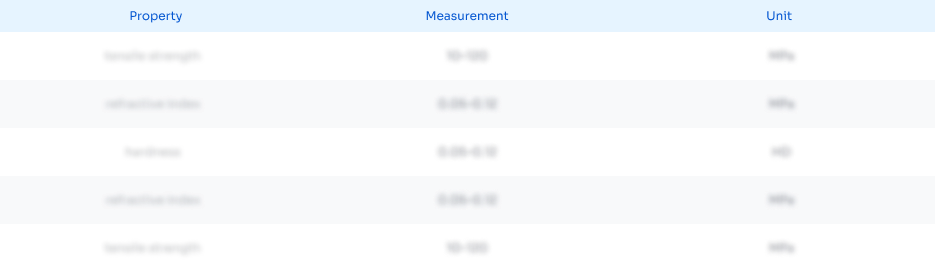
Abstract
Description
Claims
Application Information
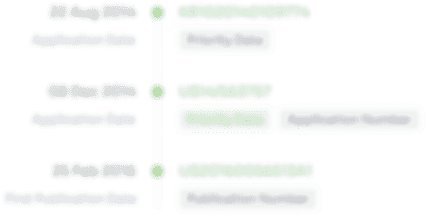
- R&D Engineer
- R&D Manager
- IP Professional
- Industry Leading Data Capabilities
- Powerful AI technology
- Patent DNA Extraction
Browse by: Latest US Patents, China's latest patents, Technical Efficacy Thesaurus, Application Domain, Technology Topic.
© 2024 PatSnap. All rights reserved.Legal|Privacy policy|Modern Slavery Act Transparency Statement|Sitemap