Structure and load transfer integrated composite material four-point bending clamp and using method
A four-point bending, composite material technology, applied in the direction of using a stable bending force to test the strength of materials, analyzing materials, instruments, etc., can solve the problem that the four-point bending load of the composite material sample cannot be effectively used and the environmental effect cannot be occupied for a long time. Coupling and other issues, to achieve the effect of simple test method, simple structure and stable working conditions
- Summary
- Abstract
- Description
- Claims
- Application Information
AI Technical Summary
Benefits of technology
Problems solved by technology
Method used
Image
Examples
Embodiment 1
[0035] Such as Figures 1 to 4 As shown, this embodiment provides a composite material four-point bending fixture with integrated structure and load, including a base plate 1, a support 2, a pressure head 4, a spring 5, a flat washer 6, a nut 7 and a long screw rod 8; The bottom plate is provided with two pairs of threaded through holes; the support and the long screw are fixed on the bottom plate; the pressure head is sleeved on the long screw and can slide freely up and down; the spring is placed above the pressure head and sleeved on the long screw above; the nut transfers the load to the spring through the flat washer.
[0036] The bottom plate 1 of the four-point bending load fixture is in the shape of a cuboid, and two pairs of threaded through holes are opened on the bottom plate, namely the threaded through hole 1 and the threaded through hole 2 . The long screw rod 8 and the threaded through hole 1 on the base plate realize tight fitting by threads. The support 2 and t
Embodiment 2
[0046] This embodiment provides a method for using a composite material four-point bending fixture with integrated structure and load carrying, including the following steps:
[0047] The composite material sample 3 is a resin-based composite material, a metal-based composite material, a ceramic-based composite material, or a sandwich structure composite material plate, and the thickness of the plate is 2mm-12mm, preferably 2mm; the length of the composite material sample 3 is 80mm-180mm , preferably 110mm, and the width of the composite material sample 3 is 10mm-30mm, preferably 13mm. The number of composite material samples 3 in the same batch is 10 or more.
[0048] Further, 5 composite material samples of the same batch were randomly selected for a four-point bending performance test, and the 5 composite material samples were bent until fracture to calculate the ultimate four-point bending strength of the composite material sample.
[0049] After assembling the parts of the
Embodiment 3
[0065] This embodiment relates to a composite material four-point bending loading fixture with integrated structure and load and its use method, which specifically includes the following steps:
[0066] Composite material sample 3 with ceramic as the matrix, sample 3 has a length of 170 mm, a width of 10 mm, and a thickness of 5 mm. The composite material sample 3 is positioned with a four-point bending fixture, and the compression amount is applied to the spring 5, so that the load strength applied by the spring 5 to the composite material sample 3 is 30% of the ultimate four-point bending load of the composite material. Place the adjusted four-point bending fixture in the ultra-low temperature bearing cooling box, set the temperature at -50°C, and test for 7 days. After the test, wait for the four-point bending fixture to return to room temperature, remove the composite material sample 3 from the four-point bending fixture and perform a four-point bending performance test, and
PUM
Property | Measurement | Unit |
---|---|---|
Length | aaaaa | aaaaa |
Elastic coefficient | aaaaa | aaaaa |
Thermal expansion coefficient | aaaaa | aaaaa |
Abstract
Description
Claims
Application Information
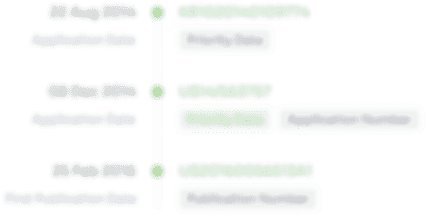
- R&D Engineer
- R&D Manager
- IP Professional
- Industry Leading Data Capabilities
- Powerful AI technology
- Patent DNA Extraction
Browse by: Latest US Patents, China's latest patents, Technical Efficacy Thesaurus, Application Domain, Technology Topic.
© 2024 PatSnap. All rights reserved.Legal|Privacy policy|Modern Slavery Act Transparency Statement|Sitemap