TPU particle foaming process
A particle and process technology, applied in the field of polymer preparation, can solve the problems of failure to reach a certain level and collapse of TPU foam structure, and achieve the effects of reducing equipment costs, complete foaming, and avoiding collapse
- Summary
- Abstract
- Description
- Claims
- Application Information
AI Technical Summary
Benefits of technology
Problems solved by technology
Method used
Image
Examples
Embodiment 1
[0032] S10 is prepared using TPU particles; S20 is infiltrated, the TPU particles are placed in an autoclave and sealed, and supercritical CO2 fluid is introduced into the autoclave to pressurize 22MPa to a saturated state, the temperature is raised to 80°C, and the temperature and pressure are kept constant for 45 minutes. Clear the gas to obtain swollen TPU particles; S30 foaming, take the swollen TPU particles out of the autoclave, place them in a hot air device at a temperature of 115°C for 45 seconds to obtain TPU foaming particles; S40 particle molding, The TPU foamed particles were placed in a container, CO2, N2 mixed gas was passed into the container, the pressure was increased to 1.5 MPa, and the pressure was maintained for 18 hours to obtain the final TPU foamed particles. The performance of the TPU foamed particles made by the above method after the insole is as follows in Table 1 Example 1 insole performance.
[0033] Table 1. Embodiment 1 insole performance
[0034]
Embodiment 2
[0036] S10 is prepared using TPU particles; S20 is infiltrated, the TPU particles are placed in an autoclave and sealed, and supercritical CO2 fluid is introduced into the autoclave to pressurize 20MPa to a saturated state, the temperature is raised to 70°C, and the temperature and pressure are kept constant for 45 minutes. Purify the gas to obtain swollen TPU particles; S30 foaming, take the swollen and unexpanded TPU particles out of the autoclave, place them in a constant temperature equipment at a temperature of 110 ° C for 30 seconds to obtain TPU foaming particles; S40 particle molding, The TPU foamed particles were dried and placed in a pressure-holding container, and a mixed gas of CO2 and N2 was passed into the pressure-holding container, the pressure was increased to 1.5 MPa, and the pressure was maintained for 18 hours to obtain the final TPU foamed particles. The performance of the TPU expanded particles obtained by the above method after being made into the insole is
Embodiment 3
[0040] S10 is prepared using TPU granules; S20 is infiltrated, the TPU granules are placed in an autoclave and sealed, and a supercritical CO2 fluid is introduced into the autoclave to pressurize 18MPa to a saturated state. Purify the gas to obtain swollen TPU particles; S30 foaming, take the swollen TPU particles out of the autoclave, place them in a constant temperature equipment at a temperature of 95°C and foam them for 20 seconds to obtain TPU foamed particles; S40 shape the granules, and After the TPU foamed particles are dried, they are placed in a pressure-holding container, CO2 and dry air are introduced into the pressure-holding container, the pressure is increased to 1.5 MPa, and the pressure is maintained for 18 hours. After the TPU particles are molded, secondary hot air foaming is performed, usually Pressing, the temperature is 70-85°C, and the time is 30-45s, so that the final TPU foamed particles have a full appearance and high gloss. The performance of the TPU fo
PUM
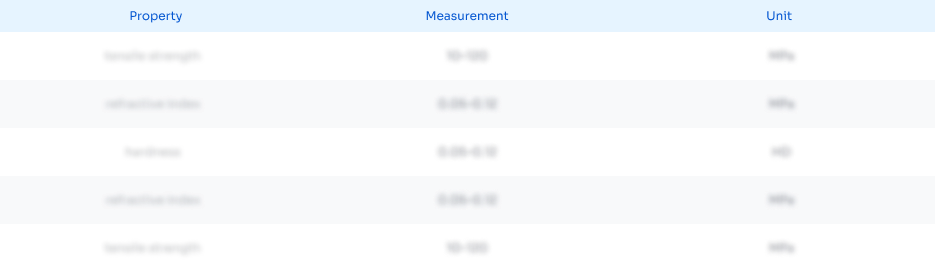
Abstract
Description
Claims
Application Information
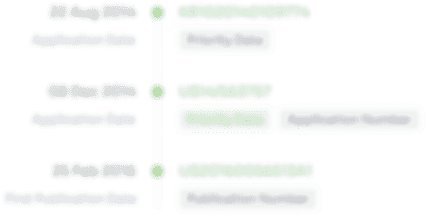
- R&D Engineer
- R&D Manager
- IP Professional
- Industry Leading Data Capabilities
- Powerful AI technology
- Patent DNA Extraction
Browse by: Latest US Patents, China's latest patents, Technical Efficacy Thesaurus, Application Domain, Technology Topic.
© 2024 PatSnap. All rights reserved.Legal|Privacy policy|Modern Slavery Act Transparency Statement|Sitemap