Method for preparing alumina catalyst, alumina catalyst prepared using same, and method for preparing propylene using alumina catalyst
An alumina and catalyst technology, which is applied in catalyst activation/preparation, carbon compound catalysts, physical/chemical process catalysts, etc., can solve the problems of reduced usefulness of crystalline alumina and reduced specific surface area of alumina dispersants, etc. The effect of improving yield, excellent catalytic activity, and high catalytic activity
- Summary
- Abstract
- Description
- Claims
- Application Information
AI Technical Summary
Problems solved by technology
Method used
Image
Examples
Example Embodiment
[0028] The method of preparing an aluminum oxide catalyst of the present invention includes: Step S1: calcining the alumina precursor to form a mixed phase alumina, the mixed phase alumina comprises from 1 to 15% by weight α-alumina, 60 to 95 The weight% θ-alumina, and 4 to 25% by weight of Δ-alumina; step S2: The mixed phase alumina is steam treated with water vapor at a temperature below the primary calcination temperature to activate mixed phase alumina; And step S3: After step S2, secondary calcination is carried out at a temperature higher than the steam processing temperature but below the primary calcination temperature. In this case, it is possible to improve the stability and activity of the alumina catalyst having a compromise based on temperature, and can prepare an alumina catalyst having high mechanical strength and high corrosion / chemical resistance.
[0029] Hereinafter, a method of preparing an aluminum oxide catalyst of the present invention will be gradually des
Example Embodiment
[0088] Example 1
[0089]Burmite was calcined at 1100 ° C for 10 hours under the air atmosphere to obtain a mixed phase oxide of θ-alumina and 20% by weight of δ-alumina by 10% by weight of α-alumina, 70% by weight of θ-alumina and 20% by weight of δ-alumina. . The mixed phase alumina was filled in the tubular reactor, and the temperature of the tubular reactor was set to 400 ° C, and then the steam treatment was performed by supplying water vapor and nitrogen to the reactor. At this time, water vapor is supplied with a rate of 0.026 to 0.1 g / min using an HPLC pump, and a mixture ratio of nitrogen gas and water vapor is supplied with a mass flow controller (MFC) at a rate of 133 ml / min (N. 2 : H 2 The volume ratio of O is 2,500: 1, and the weight ratio of water vapor and mixed phase alumina is from 0.01 to 100: 1. Further, after the steam treatment, calcined at 550 ° C for 5 hours to obtain an alumina catalyst.
Example Embodiment
[0090] Example 2
[0091] This process is carried out in the same manner as in Example 1 except for 6 hours rather than 3 hours during steam treatment.
PUM
Property | Measurement | Unit |
---|---|---|
Specific surface area | aaaaa | aaaaa |
Pore volume | aaaaa | aaaaa |
Abstract
Description
Claims
Application Information
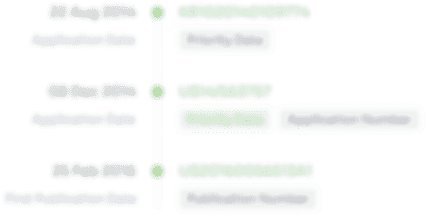
- R&D Engineer
- R&D Manager
- IP Professional
- Industry Leading Data Capabilities
- Powerful AI technology
- Patent DNA Extraction
Browse by: Latest US Patents, China's latest patents, Technical Efficacy Thesaurus, Application Domain, Technology Topic.
© 2024 PatSnap. All rights reserved.Legal|Privacy policy|Modern Slavery Act Transparency Statement|Sitemap