Catalyst for preparing formaldehyde through methanol oxidation
A catalyst, methanol technology, applied in the direction of physical/chemical process catalyst, carbon-based compound preparation, organic compound preparation, etc., can solve the problem of low selectivity, and achieve the effect of improving selectivity, improving stability and good catalytic activity
- Summary
- Abstract
- Description
- Claims
- Application Information
AI Technical Summary
Problems solved by technology
Method used
Examples
Example Embodiment
[0023] [Example 1]
[0024] 14.4 g of molybdenum oxide was added to 110ml of 10% hydrogen peroxide, and after stirring for 8 hours at a reaction temperature of 80°C, 55ml of 1M nitric acid solution was added and stirring was continued for 16 hours to obtain a peroxymolybdic acid solution. The solution was put into an autoclave and reacted at 150°C for 72 hours to obtain nanorod molybdenum oxide.
[0025] Take 23.04 grams of the above molybdenum oxide and add it to the mixed solution containing 24.4 ferric nitrate and 0.9 grams of manganese nitrate, Mo / Fe molar ratio = 1.6:1, add 10 grams of hydroxyapatite, stir for 4 hours, and place at 100°C Dry in an oven for 24 hours, and then calcinate at 400°C for 10 hours to obtain a nanometer iron molybdate catalyst named NMF-1.
Example Embodiment
[0026] [Example 2]
[0027] 14.4 g of molybdenum oxide was added to 110ml of 10% hydrogen peroxide, and after stirring for 8 hours at a reaction temperature of 80°C, 55ml of 1M citric acid solution was added, and stirring was continued for 16 hours to obtain a peroxymolybdic acid solution. The solution was put into an autoclave and reacted at 160°C for 72 hours to obtain nanorod molybdenum oxide.
[0028] Take 31.68 grams of the above molybdenum oxide and add it to a solution containing 24.4 grams of ferric nitrate, Mo / Fe molar ratio=2.2:1, add 20 grams of hydroxyapatite, stir for 4 hours, and place it in an oven at 100°C for 24 hours. Then calcined at 500°C for 6 hours to obtain nanometer iron molybdate catalyst, and named NMF-2.
Example Embodiment
[0029] [Example 3]
[0030] 14.4 g of molybdenum oxide was added to 110 ml of 10% hydrogen peroxide, and after stirring for 8 hours at a reaction temperature of 80°C, 55 ml of 1M oxalic acid solution was added, and stirring was continued for 16 hours to obtain a peroxymolybdic acid solution. The solution was put into an autoclave and reacted at 180°C for 48 hours to obtain nanorod molybdenum oxide.
[0031] Take 51.84 grams of the above molybdenum oxide and add it to the mixed solution containing 24.4 grams of ferric nitrate and 0.74 grams of tin nitrate, Mo / Fe molar ratio = 3.6:1, add 30 grams of hydroxyapatite, stir for 4 hours, and put it to 100 It was dried in an oven at ℃ for 24 hours and then calcined at 550 ℃ for 6 hours to obtain a nano-iron molybdate catalyst, which was named NMF-3.
PUM
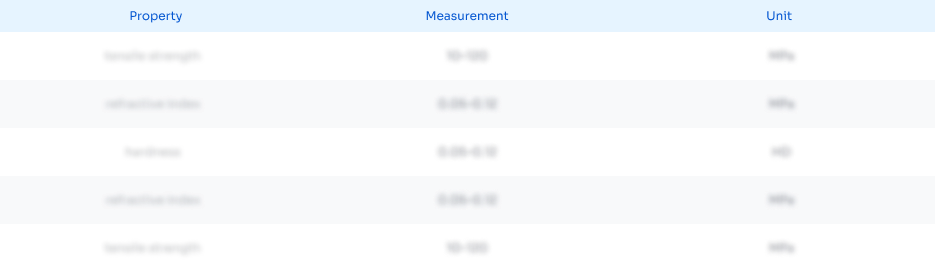
Abstract
Description
Claims
Application Information
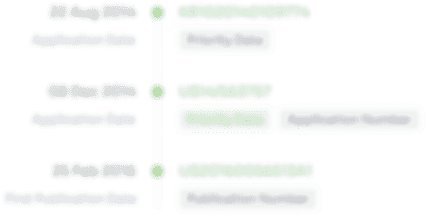
- R&D Engineer
- R&D Manager
- IP Professional
- Industry Leading Data Capabilities
- Powerful AI technology
- Patent DNA Extraction
Browse by: Latest US Patents, China's latest patents, Technical Efficacy Thesaurus, Application Domain, Technology Topic.
© 2024 PatSnap. All rights reserved.Legal|Privacy policy|Modern Slavery Act Transparency Statement|Sitemap